BD Energy
You Can’t Control What You Don’t Understand
While South African businesses were spared from Eskom’s proposed 32 per cent tariff hike, energy regulator Nersa nonetheless allowed the utility to increase tariffs by 18.65 per cent. Although not as crippling as it could have been, this remains another heavy expense for local companies to foot, especially as they use between 15 000 and 50 000 kilowatt hours of electricity annually, depending on the size of the company.
Businesses are already paying very large amounts for their electricity consumption, and you can add to this the further costs they are hit with each month should they exceed their notified maximum demand (NMD) limit. Businesses can no longer afford for their energy use to remain unmanaged, particularly in light of continued turbulent economic conditions.
As the old cliché goes, “You can’t manage what you can’t measure.” So if businesses don’t know what is contributing to their electricity bills, it becomes very difficult for them to control these and to understand how to reduce costs.
Getting smart about measurement
To illustrate this, we had a client that was spending upwards of R120 000 every month on electricity, but did not know what was contributing to this cost. While they were aware that approximately R30 000 was going to NMD penalties, which is money straight down the drain, of the R90 000 for consumption, the organisation could only guess. At the same time, they were spending hours trying to compare consumption data against their utility bill manually.
The best way for business owners to start tackling spiralling electricity costs is to implement managed smart metering at several key points in their electrical network. This enables them to gather and analyse real-time electricity consumption data. Once they can identify exactly where energy is being consumed, they can ensure that measures are put in place to reduce wastage of both money and energy.
It is also worth noting that while everyone has their part to play when it comes to reducing energy consumption, relying on the company’s employees to change their behaviour often doesn’t yield optimal results. Unless electrical load management is automated, a business’s ability to reduce its consumption costs is
fairly limited.
When the lights go out
Adding to the above expenses, ongoing load shedding is losing businesses millions in revenue, as they are simply unable to operate during outages, not to mention the additional consequential damage to equipment and machinery. All told, this is estimated to be costing the country’s economy some R4-billion per day. It is therefore unsurprising that a great number of companies are actively seeking alternative power supplies, in order to avoid reliance on the unstable grid. In fact, the commercial and industrial sectors account for about 70 per cent of all new rooftop solar photovoltaic (PV) installations at a national scale.
Currently, many solar PV systems have batteries that can typically only provide a few hours of backup (if sparingly used) because they have limited capacity. Large batteries are very expensive. While solar PV provides a measure of energy cost reduction, it is battery storage that provides the critical energy security to make sure machines and computers are still running.
However, it is essential to have load management to prevent the battery from draining unnecessarily, considering that something as simple as an employee heating their leftover pizza in the company kitchen at lunchtime could flatten the reserve, crippling the business.
In today’s business climate, companies are primarily concerned about reducing their upfront capital. However, they need to consider all the costs associated with unmanaged consumption, including their environmental, social and governance and carbon footprint reduction objectives, as well as the most basic and necessary capability: that of being able to keep trading and servicing their customers.
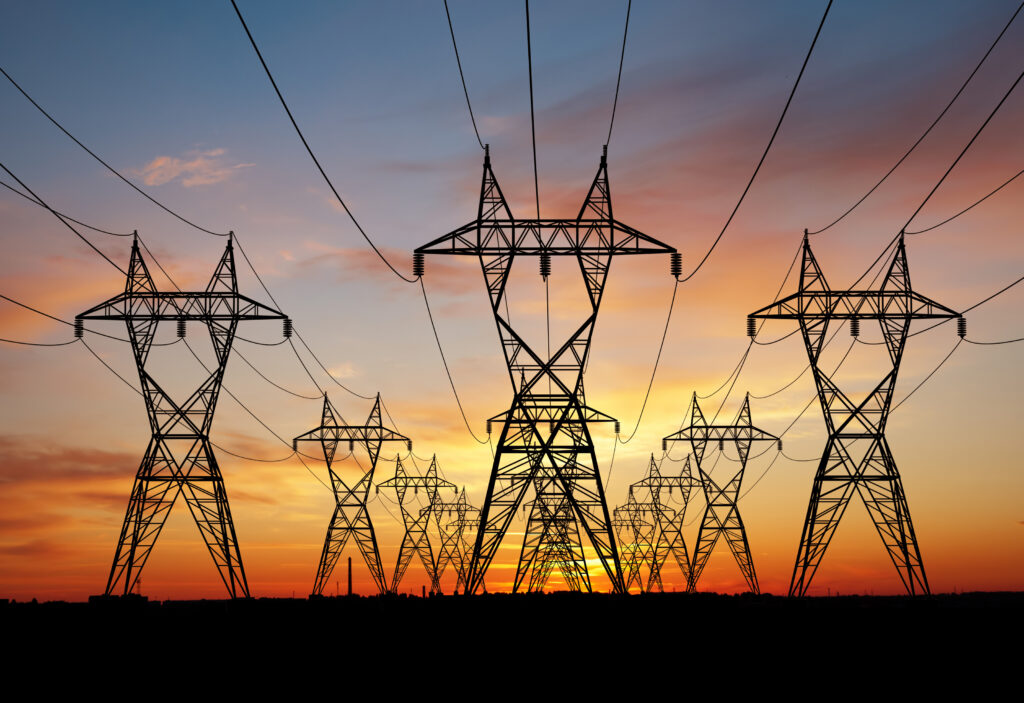