BD Manufacturing
Everything Everywhere All At Once
Surviving in today’s globalised, highly competitive marketplace requires you to work smart. To do so, you need maximum visibility of your manufacturing operations. An enterprise resource planning (ERP) system logs all supply chain transactions in one place, creating visibility, improving governance and providing the information you need for data-driven reporting. It facilitates control of business processes and co-ordination of activities across the supply chain while capturing relevant financial transactions in parallel to help measure how the business is doing. If implemented correctly, an ERP system can fuel increases in efficiency and business effectiveness.
Looking forward
At its most basic level, an ERP system logs transactions through the supply chain, from procurement through manufacturing, inventory, distribution, sales and delivery to customers. In parallel, it does the financial journals in the background.
Having visibility of your transactions alongside the movement of products through the manufacturing process gives you visibility, allowing you to draw insights and make more accurate forecasts. Forecasting is enabled by forecasting algorithms contained in ERP and other systems. These take care of the statistics, working with historical demand, trends, seasonality and bias captured in the ERP system to drive the forecasting process. You can do that in a spreadsheet, but these algorithms go one step further by measuring their own forecast accuracy, examining the previous twelve months and then gauging the accuracy of the twelfth month’s prediction in terms of the data from the prior eleven.
Planners can rely on forecasts as long as they’re 90 per cent accurate or higher – typically, this applies to key value items and fast movers. However, there will also be products with low accuracy, probably due to infrequent or random demand. Letting ERP systems manage the high-accuracy items frees planners to focus on how best to improve forecast accuracy for the less predictable items.
Streamlining inventory
More accurate forecasting creates a cycle where planners either get closer to the customer to understand when slow movers are required or, more likely, they amend ERP inventory management parameters, such as order point, order quantity and lead time to supply, to keep stocks at a sensible level that covers the uncertainty of these products. Thus, the system manages the stock mix more effectively, ensuring stock cover (for example, days of supply or a fair quantity) is balanced to avoid inventory investment in the wrong items while increasing customer service for all items.
The objective is ultimately to manage inventory so total stock holding is reduced while customer service is maintained or even improved – a win-win situation. The essential thing to understand is that where there is an uncertainty of demand levels or supply, this must be buffered by holding more stock. By removing as much uncertainty as possible with ERP tools, costs can be reduced and service improved.
Productivity and distribution
ERP doesn’t just manage inventory, but also helps with production and distribution. Taking the improved demand plan and dropping this into production planning in your ERP system ensures that the right production jobs are scheduled at the right time, and overloads or capacity issues are relieved through rescheduling or adding shifts to ensure that what is planned for can, realistically, be produced effectively. An effective production plan results in less wasted time and gets more production through the same machine tools, processes and people; this is the essence of increasing productivity.
Additionally, this new production plan is used to drive the ERP materials plan, procuring and supplying the right materials to production for these scheduled jobs. This means better co-ordination of equipment, material supply and worker throughput. And more throughput from the same resources means lower cost of production as total operation cost is spread over a larger number of items produced.
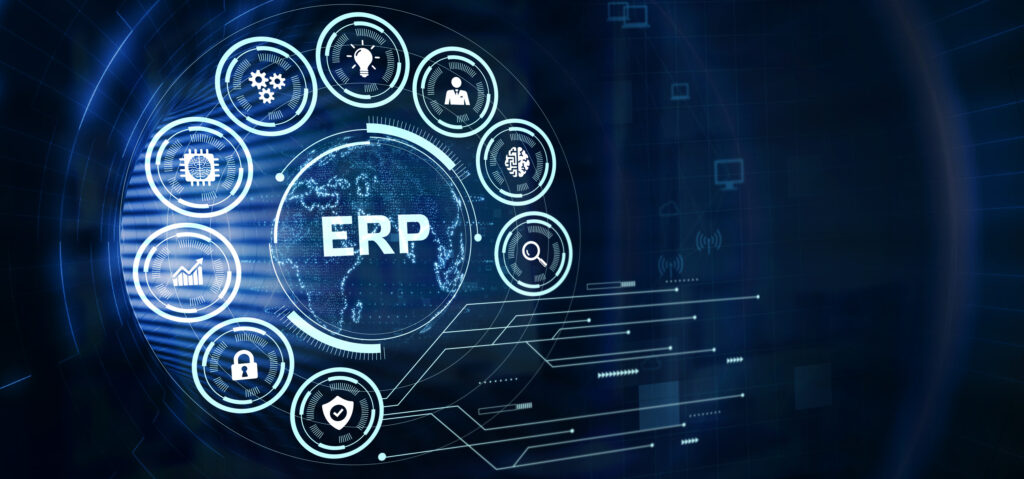