SA Mining
Safety Is A Key Step On The Road To Productivity
As one of mining’s critical performance areas, blasting has a special respect for best practice in safety, says Ramesh Dhoorgapersadh, general manager for Safety, Health, Environment, Risk and Quality (SHERQ) at blasting and explosives leader BME, a member of the JSE-listed Omnia Group. Indeed, proven safety performance and demonstrable systems are today a basic pre-requisite to earn contracts from leading mining companies.
“This means ingraining safety into every activity, in line with recognised standards and procedures,” said Dhoorgapersadh, highlighting the company’s Safety for Life brand. This guides every step in the company’s process – from raw material sourcing and emulsion manufacturing through to final blast initiation. He emphasised the negative potential impact of any blast-related delay or incident that could affect a mine’s smooth operation.
“Any delays – including those from safety-related incidents – can cause disruption, while a Section 54 notice can bring an entire operation to a halt, with massive financial implications,” he said. “For this reason, no aspect of the blasting function can be left to chance – and BME ensures this with its thorough safety management system.”
The result has been plain to see, with the company’s recorded case rate reaching a record low of 0.05% for the last financial year. This represents a world-class achievement in the blasting sector, and also places BME among the ranks of the best safety performers in the local industry. This follows the company’s earlier recognition for safety, health and environment performance improvement at the Chemical and Allied Industries Association Awards.
“Our blasting philosophy – through our innovative products and leading initiation technologies – aims to optimise the productivity of our customers’ mining operations,” he said. “Underpinning our ability to do this is a foundation of safe practices that mitigate our customers’ risk – by aligning with their own safety protocols and broader regulatory requirements.”
Dhoorgapersadh highlighted the extensive footprint of BME’s network across Southern Africa in particular, where emulsion explosives, accessories and equipment are constantly moving between manufacturing facilities, factories and mine sites. Governing every step of these journeys is a detailed safety system – ensuring every stakeholder’s safe return home at the end of each day.
“Even across borders, our safety culture is shared, ingrained and enforced among all BME employees and contractors alike, so that we can apply and embed our safety learnings wherever we operate,” he said.
The success of BME’s results reflects the broad approach to occupational wellness – supporting the health of employees with regular monitoring by an occupational doctor and nurse. Inspections by medical professionals are part of a medical surveillance programme of all the company facilities. This would include site visits to check the responsible handling of hazardous chemicals, constantly ensuring that personnel are not at risk.
Safety and security are also given top priority in the design of BME’s products and equipment. Its latest AXXIS Digital Initiation Systems are a case in point. Whereas most electronic detonators rely on only one basis of safety for logging and testing the detonators, AXXIS will now have two.
“This allows us to use low voltage, which is below the firing sensitivity of the fuse head, during programming and testing of each detonator from a hand-held logger,” he said. “This inherently safe method for programming and testing ensures the detonators are inert while people interact directly with them.”
Should a higher voltage be applied by a different device, the second safety measure ensures that detonators are safe through their split power supply – so that the main firing capacitor cannot be charged during programming and testing. Security is provided by robust communication protocols between detonators, loggers and blast boxes.
“The blast command has added reliability cross-checks, thus preventing the risk of uncommanded initiation,” said Dhoorgapersadh.
The key logger principle is another important security feature in AXXIS and allows a blast to proceed through the process from testing all detonators in the blast to charging the firing capacitors, and firing the blast. The key logger authorises the system to continue through the stages of blasting using PIN numbers, while only one key logger can be used on each blast.
He noted that BME’s electronic detonation systems were tested in line with SANS 551 tests for detonator safety and were accredited in terms of ARP SANS 1717.
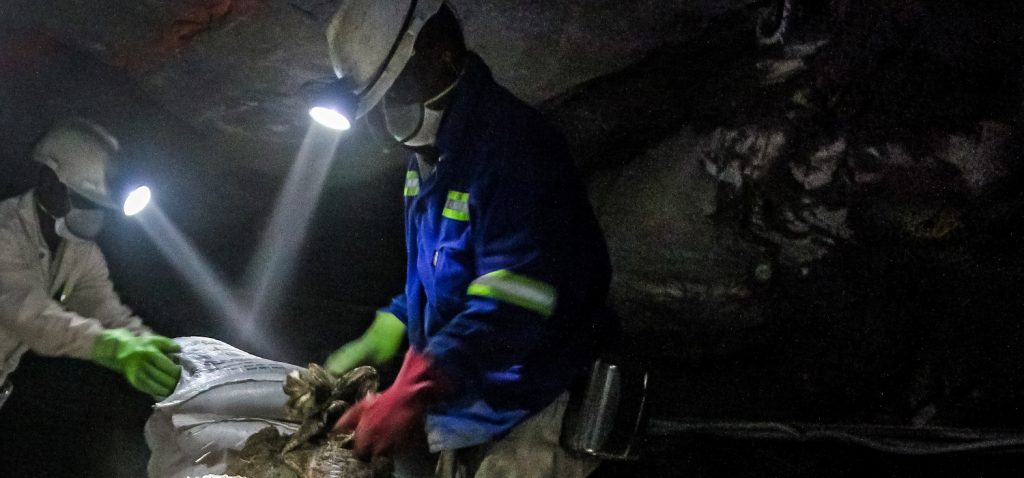