SA Mining
On The Trail Of Zero Harm
Contrary to popular perception, the mining industry has not been slow in its adoption of digital transformation. In fact, it is an industry that for some time has been shifting its business models in a digital direction, but for a far better reason than most businesses.
Whereas most organisations leverage digital technology to assist in optimising processes, or in maximising the value of existing applications, the mining industry in South Africa – which operates on the principle of zero harm – has been using digital transformation to help safeguard employees in a number of ways.
According to Ingrid Osborne, co-founder and CEO at Saryx Engineering, digital technologies offer a safety aspect right from the start of a project. She notes that contractor management, and the management and control of safety files, remains time-consuming if it is still a manual process, while also being resource-intensive and unreliable.
“Often, when an incident occurs, relevant contractor information is not immediately at hand or easily accessible, creating uncertainty that could possibly lead to fines or penalties. For this reason, Saryx created HSEC Online®, a solution that digitises the cumbersome manual safety file system and streamlines the contractor management process.
“Through this digital platform, mines – like other organisations – can action requests, submit documents for approval, and track compliance levels. The latter from an individual and company level, through to a site level and finally to a group level,” she says.
“Zero harm can always be tracked through to percentage compliance. A compliant company is a safe company, especially when it comes to the compliance of people and equipment. HSEC Online® allows mines to digitise checklists and define priority documents for certain occupations and job descriptions, thereby ensuring that when tasks are executed, the necessary processes are followed and tracked to completion by a qualified person.”
She says collecting data in the form of actual plant information, pictures or documents, for all these actions, adds certainty and transparency. And doing this on a regular basis, with reminders, creates a consistent history of events which shows credibility.
“When an accident occurs on a mine, it generally involves a critical injury and/or death. During these stressful times, the burden of proof lies with the mine to ensure that they have done everything practically and legally required of them to prevent such an event from occurring.
“It is essential therefore to be able to confidently access the information relating to the company, person(s) or equipment involved. Fast search-and-find algorithms ensure that these documents are immediately accessible and printable as evidence. Recommendations are easy to implement and come into effect immediately.”
In fact, she adds, with HSEC Online®, there is never a valid reason to have expired or invalid documents within a system. The solution has the necessary system checks to ensure this does not happen built into it.
“This is a system that reduces workloads by up to 90% and reminds you of things to come, actions to take, is proactive rather a reactive, and is super easy to manage. It boils down to the simple fact that it is incredibly powerful for an organisation to have real-time line-of-sight of compliance for every company they oversee,” says Osborne.
Going virtual
The Dekra Institute of Learning, in collaboration with Virtutec, has recently launched a virtual reality (VR) and 3D PC based e-learning platform, designed to train people working in dangerous industries like mining.
Denis Vaden, COO of Virtutec, points out that VR is a highly effective technology for teaching safety training, because the trainers don’t have to put the person being trained through dangerous procedures or processes. This is especially desirable and helpful for individuals who have not had any experience regarding the specific processes or physical environment. The VR experience simulates the real-world situation as closely as possible without having to experience potential danger.
“By making use of a VR headset, the trainer is able to simulate the relevant environment, ensuring it mirrors the real-life situation as closely as possible. Thereafter, when the trainee is placed in a real-world situation, there is a familiarity with systems and processes, as well as the environment,” he says.
“In addition, VR technology promotes efficient and effective knowledge retention. A survey from global professional services company PwC has found that an individual’s knowledge retention via VR learning can be almost 300% improved, compared with many other forms of training. This is because learners are in a situation in which they are immersed in the environment with no distractions, which facilitates a deeper learning process.”
Vaden notes that VR training can be very cost-effective, especially when compared to the much higher costs of simulation systems, which provide training for only one person at a time. VR training, on the other hand, allows for multiple headsets to be acquired and used to train multiple trainees simultaneously. In this way, VR training can be highly leveraged for teaching mine safety, as it scales significantly better than some other forms of training.
“VR training can be custom-developed with specific training modules in mind for specific companies, who guide us through their standard operating procedures and requirements,” he says. “We are able to scale some of our existing products and training programmes, for example the working at heights programme. This means that the existing programme can be leased, whereby the software can be rented to the mine as a monthly package, which further assists with cost savings.”
Christopher Mörsner, head of the training division at Dekra IOL, says: “Dekra IOL is currently engaging with various mines, and the VR training is used here to simulate the operation of heavy equipment, where it is costly to buy the equipment that learners need to be trained to use.
“Without VR technology, mining processes on the ground must actually be stopped in order for training to take place. It is much easier and more cost-effective in this regard to use the VR headsets. In addition, the VR training supports safety training – simulating real-life situations and demonstrating potential consequences. VR technology is an extremely effective medium in which to train people for situations where safety is paramount – such as on a mine.”
Digital technology onsite
Recent global safety reports suggest that there has been a gradual but steady improvement in mine safety over the past decade. According to Ramesh Dhoorgapersadh, general manager for safety, health, environment, risk and quality at BME, safety is something that needs to be ingrained into every activity, in line with recognised standards and procedures.
“The blasting philosophy of BME is expressed through innovation in our product development and our leading initiation technologies. This also means aligning our policies with customers’ own safety protocols and broader regulatory requirements,” he says.
Tinus Brits, BME’s global product manager – AXXIS™, adds that electronic detonation systems play an important role in achieving safe blasting. They allow detonators to be accurately initiated within milliseconds of each other, staggering the energy release rather than having five or six holes detonating at the same time. Reducing the charge mass per delay ultimately reduces the resulting vibration.
“We design our electronic detonators in such a way that key blast impacts are both measurable and predictable. With our integrated blast planning software, mines can simulate each blast before it is implemented – so that they can predict aspects like ground vibration, thereby ensuring it will be within the required parameters.”
He emphasises that mines apply world-class standards in this regard, such as the US Bureau of Mines blast-induced ground vibration criteria. These include the requirement that any blasting in the vicinity of communities, structures, houses, roads or other receptors requires a minimum safety radius.
Where BME conducts blasts on behalf of customers, therefore, it applies a blasting radius of 1km from any people or communities, and 500m from any material that might be negatively affected.
“For every blast, seismographs are then used to measure the resulting ground vibration and air blast. This confirms that the blast did indeed achieve the simulated design parameters, to fall within the regulated limits,” says Brits.
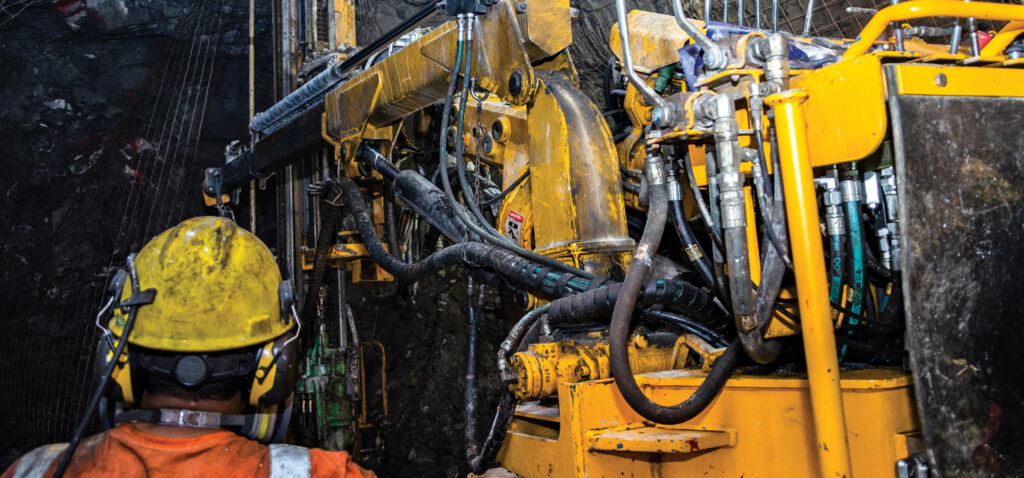