SA Mining
Is Mining Investing Sufficiently In Training And Skills Development?
SA Mining recently caught up with Ogi Williams, associate director at In On Africa (IOA) and Maritha Erasmus, CEO of Managing Transformation Solutions (MTS), to chat about the effects the changing environment is having on training and skills development in the local mining industry.
Is South Africa investing sufficiently in training and skills development, especially in the mining sector?
An argument can always be made that additional investment is needed to develop a trained and ready workforce. Though considerable emphasis has been placed on increasing the available funding going towards training and skills development, there are evident mismatches between the types of skills that are taught within the sector, and those skills required to ensure that the workforce is ready for modernised mining techniques. External pressures that need to be taken into account include: the proliferation of new technologies which are misaligned with skills and training initiatives; current retrenchments in the sector given low demand; and transformation targets which are placing additional stress on the industry to align with the latest revision of the Mining Charter. The key question to ask is whether the current skills available in the mining industry are being sufficiently developed in order to meet future needs.
The MTS Insite platform provides information of the skill levels of those employed in the mining industry. MTS is the developer of the social sustainability technology platform Insite. According to the data, the HET (higher education and training) education levels of Paterson C and above are indicative of older employees with more experience and less education, whereas at the general education and training (GET) and further education and training (FET) educational levels of the Paterson A and B levels, employees should be read with the average age of these employees as well – predominately youth (<35). In terms of Paterson levels – the job grading system used to grade roles on the basis of decision making, and freedom to act – 76% of all employees within the sample assessed, and 94% of all employees in the top 10 core positions, are only at Paterson level A or B. This is supported by data provided by the Mining Qualifications Authority (MQA) where the majority of workers have a GET/FET education with only 14% of employees in the mining sector equipped with a post-matric qualification.
How much have mining companies invested in training and skills development in 2017?
Cumulatively, according to the Minerals Council, some R6-billion was invested by the mining industry in the 2017/18 period. As noted, however, even though considerable sums of capital are being invested in the sector, the return on this investment is still low given market volatility and fluctuations in mineral demand.
In terms of investment in training and skills development, how does South Africa compare with global entities?
At the moment all the major global mining companies are taking stock of what’s going to be needed in the coming decade and beyond. The impact of digitalisation within mining is going to be far reaching, and unless mining companies evolve out of their current models they won’t survive. If you look at other major mining markets like Australia, Brazil, Canada and Chile, all are making headway towards investing for the future. The skills needed going forward are changing rapidly, from self-driving trucks to enhanced drilling technologies, and labour needs to match these needs in order to maintain industry competitiveness. In South Africa, we are behind in terms of innovating towards skills development with pressure coming from government to transform and diversify the industry, particularly at senior management level.
We continue to be labour-intensive in comparison to other major mining markets and according to the latest available mining figures from the Minerals Councils there are over 460 000 people employed by the mining sector. In comparison, Australia employs less than half that number of people as does Canada. What’s interesting to note in these two comparisons is that if you take into account the downstream value added in the mining sector in both countries, it is considerably larger than our own. The education level of our workforce essentially keeps us in a perpetual trap of mining more minerals through less efficient ways which is costing the industry more, while other mining markets are extracting less ore more often and more efficiently. It’s not about how much we invest, it’s more about how we can progress the labour force as effectively as possible through education such that we start filling the need for more skilled occupations which we so desperately need. This is reflected in the latest available data from the MQA on the proportions of the labour force with education – over two-thirds (69%) have a level of education between grades 4 and 12.
In terms of skills shortages, which are the areas that are in need of investment?
For one, there are still a number of occupations within the mining sector that are difficult to source labour for. The 2017/18 iteration of the MQA Sector Skills Plan (SSP) has noted that occupations such as mining manager, mining planner, mining engineer and rock engineer, among others, are positions that are still very difficult to fill. There have also been considerable fluctuations, and in some cases a decline, in terms of the numbers of qualified personnel coming out of training programmes. Data from the MQA notes fewer certificates being issued for occupations such as advanced mine surveying and advanced mine valuations. On the positive side, though, over the past year there has been a considerable rise in the number of certificates issued for positions in mine environmental control – which is reflected by government’s emphasis on reining in the environmental impact of mining.
In mining, which are the scarce skills sets and what is industry doing to meet these skills?
One of the key drivers for the skills shortages is the lack of sufficient experience at senior levels of mine management within the sector as well as the undesirable geographic locations of mines in SA, driving up salary requirements for these positions. Part of the reason for the lack of experienced mine managers, engineers and planners is the current economic recession in South Africa which has resulted in a high number of skilled and experienced people immigrating to other jurisdictions. The mining industry has increased its investment in bursary programmes and graduate development to address these skills needs, however the programmes will not alleviate the skills shortages at management levels in the short term.
Further scarce skills as noted in the Paterson C band include diesel mechanics, fitters, boilermakers and instrument mechanics not having sufficient knowledge and experience in updated technologies, as well as adequate STEM (science, technology, engineering and maths) skills for the modernised mine environment. The mining industry and government need to focus on the development of bridging programmes through which working adults can be introduced to STEM skills to ensure that their skills remain relevant in the working environment of the future.
How are the requirements of the Fourth Industrial Revolution impacting on training and skills development? Is there a need for a NEW skills set?
The main supply-side concerns revolve around basic education such as low levels of maths and science and insufficient access to career awareness. Within the technical and vocational education and training (TVET) college sector there is a lack of practical training along with outdated curricula. Some of the primary reasons for the current skills gaps include:
Maths and science and career awareness events should be monitored for impact, given the importance of the subjects as building blocks for the majority of occupations in the sector. Similarly, technological change remains at the forefront of the sector’s ability to become as safe, healthy, efficient and sustainable as possible.
New, sophisticated technologies are transforming the sector’s operations. As a result, the type, level and mix of skills required is starting to change, affecting occupations including rock drill operator, blaster, drill rig operator as well as most of the artisan trades. Upskilling and reskilling programmes are needed so that employees are trained in new mining processes that will extend the lifespans of mines.
What are emerging trends in training and skills development in the mining sector?
Upskilling and training will be required for all skills levels of workers, including managers and supervisors, to ensure a smooth transition to mechanisation. A focus on AET (adult education and training programmes up to level 4 as a way of improving literacy and numeracy levels will be important to prepare existing and potential employees to operate new machinery and coordinate new processes).
What are the key takeaways from the Mining Trends Report 2018?
The South African mining industry is an important employer of vulnerable groups within the country. The trend report found that there has been a significant increase in the level of youth, female and localised employment within the sector. This has largely been as a result of the drive towards social sustainability and transformation.
However, despite the high number of youth employed with FET qualifications, the majority of the workers were employed in unskilled and semi-skilled positions, with the trend becoming more acute when compared over a period of time. The majority – up to 80% – of employees at a mine are also employed in core mining positions, with a concentration noted into fewer positions. In 2012, 27% of all core mining employees were employed in the top 10 core positions compared to 40% in 2017. The evidence would suggest that the skills and expertise within core mining positions has become more concentrated over the five-year period.
What measures can South Africa put in place to meet changing needs?
If South Africa is to remain competitive in the global mining industry, there is a need to start instilling a push towards higher education much earlier on during the school years in preparation for future mining needs. The global emphasis on environmental impact as a result of mining activities is another key driver of the greater modernisation and mechanisation of the industry. Decreasing the carbon footprint on the back of mining requires the use of new and improved technologies, which in turn requires higher skilled labour. Mine safety is another key concern in South Africa as ore is buried deep underground which proves increasingly dangerous for direct human extraction.
Modernisation of the industry needs to also permeate into downstream activities with greater value-addition being drawn from mining, however a core challenge that remains is inadequate access to infrastructure such as water and electricity in semi-urban and rural communities. The various investments being dedicated towards skills development should also be directed at primary school level where the foundation needs to be strongest. Coupling this with the introduction of new technologies at schools will also be vital to instil a strong technologically driven mindset that can then translate into actionable change and meaningful contributions in later years.
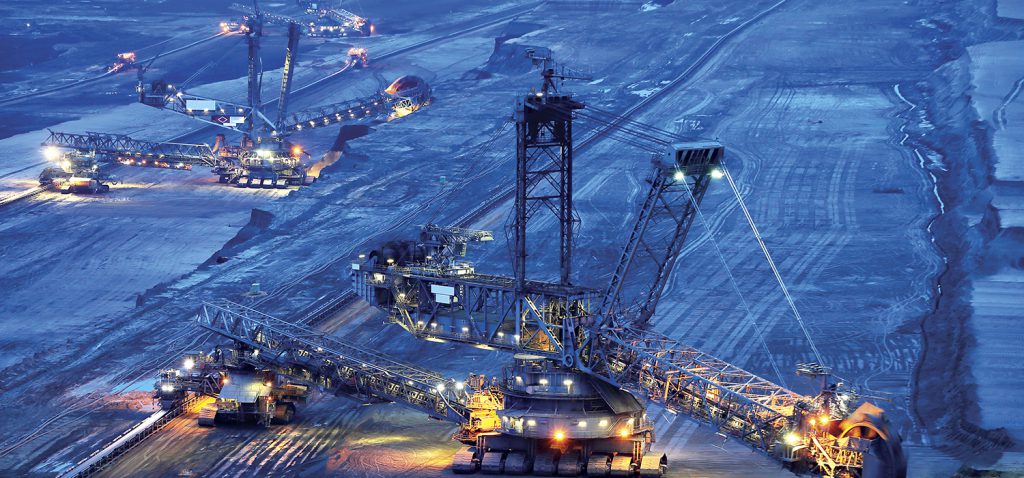