SA Mining
Boosting The Downstream With Better Blasting
There is little doubt that the digitisation of the mining industry is delivering huge benefits to the industry. New digital tools and quality electronics are making mining, in particular the blasting and explosives arena, more efficient and less carbon-intensive.
More efficient, higher quality blasts ensure better fragmentation, so that less energy is consumed in downstream stages like loading, hauling, crushing and milling. More crucially, less energy directly results in lower carbon emissions when coal- or diesel-fired electricity is used. At the same time, larger blasts mean fewer mine stoppages, allowing a more streamlined mining process.
According to Ralf Hennecke, managing director at explosives manufacturer BME, one of the challenges, in terms of negative impacts, of blasting in opencast mines and quarries are ground vibrations coupled to the risk of fly-rock, not to mention noise and dust creation.
“Fortunately, blasting technology has evolved considerably in recent decades, allowing blasting to be much more controlled. BME’s sustainability contribution takes place on various levels.
“In the manufacture, transport, storage, and application of our explosives, we follow strict environmental policies that ensure no negative impacts in our supply chain. Even in our production facilities, we are moving towards renewable energy to lower the carbon footprint of our operations,” he says.
“Perhaps the most important impact, though, is reducing the energy requirements of our customers – the mines themselves. By facilitating quality blasts, we streamline the loading, hauling and processing phases of mines, through achieving the right fragmentation of rock. This cuts energy consumption and hence carbon emissions at mine level, a growing strategic imperative for the sector.”
Green emulsions
Hennecke notes that blasting is a fundamental part of the mining process, and a quality blast will generate predictable consistency, muck piles, and dilution. This makes everything easier, from digging to crushing. In contrast, a poor blast generates pain points throughout the production chain.
“An important innovation in BME’s emulsion explosives is the incorporation of used oil as a fuel agent, which makes for a greener product and protects the natural environment from contamination. Used oil presents a risk to both water and land, if it is not disposed of in a responsible way,” he says.
BME has developed not only the technology to use this waste product in its explosives, continues Hennecke, but also provides a valuable and highly controlled used oil collection service for its customers and other oil users.
“It has also been important to remove dangerous greenhouse gases that could be generated in the explosives production chain, such as nitrous oxide (N2O) – which is almost 300 times more harmful to the climate system than carbon dioxide.”
As a member of the JSE-listed Omnia Group, BME benefits from Omnia’s Environox plants, which scrub 98% of the N2O from the production facility’s absorption tower, he says.
“Like our customers, we have taken a proactive approach to driving sustainability in our own operations – which will also benefit the country’s energy supply constraints.”
For example BME has installed solar power at its manufacturing facilities to ensure continuous production capacity. This strategy is in line with the Omnia Group focus on sustainability.
Focus on safety
Innovation and technological development have been an essential component of business strategy in every sector across the globe, says Ashlin Pillay, product portfolio manager – Electronic Initiation Systems at AECI Mining Explosives.
“Mining is no exception. Technological progression is yielding far-reaching improvements in safety, sustainability and operational efficiency throughout the value chain. In South Africa and globally, AECI Mining Explosives is recognised as being at the forefront of innovation,” he says.
“We pride ourselves on developing innovative solutions in the initiating systems and commercial explosives space. That’s how we remain at the forefront of technology and constantly pursue sustainability and continuous improvement.”
Environmental, social and governance (ESG) principles are fundamental elements in the way that AECI Mining Explosives conducts its business across all its operations and product ranges, says Pillay. Tenacious consideration is afforded to all three aspects of ESG.
“When it comes to safety, we have a solution that enables customers to build their very own blast library, detailing blast design parameters, which may be used for future blasts in similar geological conditions during blasting. This is an important safety aspect, but can also help to improve operational efficiencies.
“Other solutions focus on safety and operational efficiencies and improved blast efficiencies, which irrefutably contribute to the environmental aspect of ESG. Thanks to long-range communications capabilities, we are also able to reduce on-bench harness wire consumption, while detailed blast logs generated by the device assist with governance, by improving reporting and compliance,” says Pillay.
Looking downstream
BME indicates that blasting has a particularly important role in the sustainability of mining and mineral processing, as it is an early stage that can impact positively on the energy efficiency of subsequent stages. This contributes significantly to reducing mines’ overall carbon footprint – which today is a key imperative for the sector.
“Among the main contributors to blasting’s sustainability impact are BME’s electronic detonators and related digital technology. The evolution of electronic detonators has transformed the blasting process, making blast timing progressively more precise, reliable, and flexible,” says Hennecke.
“This allows blasts to be carefully designed and timed to optimise rock fragmentation – as well as to more clearly separate ore from waste – to make the loading, comminution, and extraction functions more efficient. Emulsions themselves also contribute to blast flexibility, through the ability to adjust their density, and hence the power they deliver at different levels of the blasthole.”
Achieving the right fragmentation during blasting, he says, means that less energy needs to be consumed downstream, particularly in energy-intensive activities such as loading, hauling, crushing, and milling.
“Electronic initiation systems such as our AXXIS solution also create the potential for larger surface blasts, allowing more detonators to be used within a single blast sequence.
“During every blast, mines must clear all equipment from the blast area and halt operations, so the fewer the blasts, the better. By having fewer blast cycles, mines can reduce their downtime and improve their overall productivity and commercial sustainability,” says Hennecke.
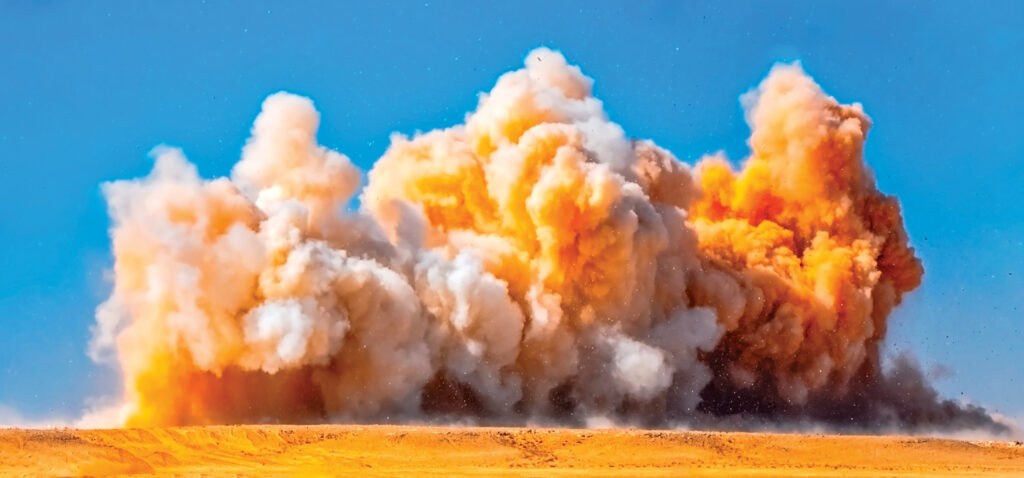