SA Mining PR
Wessels Mine Cable Belt Drive System Upgrade Overview
The Cable Belt currently hoists rock up a 14.5° incline, 1675m long, divided into two sections. Both of the driving ropes are 45mm in diameter, and with the upgraded system, will run at a maximum speed of 3.3m/s with a belt load of 84.2 kg/m. This results in a peak rope pull of 30 tons per rope.
The complete electro-mechanical system is being replaced with modernised components and electronics. The new components comprise of two independently powered drive wheels 3.5m in diameter, hydraulic power pack, disc brakes, with a Flender P2LV25 Planurex II planetary gearbox, Flender Rupex RBS 400 brake disc 710 input coupling, Flender Zapex ZWN 690 output gear coupling and a 785kW motor driving each wheel. The new control system consists of variable speed drives, Motor Control center (MCC) panels, drive transformers, and a PLC.
In addition, a 37kW 1m diameter Snatch Winch was designed and manufactured, to enable pulling the drive ropes for rope replacement and maintenance. The snatch winch is positioned in the middle of the two drive wheels facing the incline shaft.
Tech Edge designed, sourced, and assembled:
-Two 3.5m diameter Drive Wheels
-Supporting bearings and pedestals
-Hydraulic Power Pack
-Main Brake Units
-High-speed Brake Units
Siemens was able to propose a complete integrated solution offering based on their strong electrical and mechanical drive train competence. With Siemens close engagement with Wessels Mine and Aurecon an evaluation of a range of technical solutions for the upgrade was introduced due to the mine’s aging conveyor drive system. This project was materialised in collaboration with the mechanical design and fabrication expertise of local partner TechEdge.
The project highlights the benefits to the industry of partnering closely with Electrical and Mechanical Original Engineering Manufacturers (OEMs) to minimize project integration and coordination risks from the earliest stages of project planning. This approach leads to reduced implementation schedules and lifecycle cost as technical interface risks are eliminated at the outset.
Close coordination of workshop assembly and testing activities by the project partners offer the customer greater convenience, while at the same time minimising the risk of on-site commissioning delays. Siemens is proud to partner with South32, Aurecon and TechEdge to deliver a high impact solution that will secure the operational reliability of Wessels mine for decades to come.
The complete Drive System is currently assembled at TechEdge’s facility and ready for the Customer Factory Acceptance Testing in September 2018. Onsite installation is planned to start in February with Commissioning due in April 2019.
The official launch will take place at the Tech Edge premises on 27th September at 10h00.
More about Siemens drive technology:
SINAMICS G150 cabinet units have been designed for variable-speed drives in machine building and plant construction. They have been specially tuned to the requirements of drives with quadratic or constant load characteristics with medium performance requirements without regenerative feedback. The control accuracy of the sensorless vector control is suitable for most applications, and additional actual speed value encoders are therefore superfluous. SINAMICS G150 offer an economical drive solution which can be matched to the respective customer requirements by a wide range of components and options.
More about Flender gear unit:
The standard solution PLANUREX series was developed for applications that place high demands on compactness, quality and price-performance ratio. This makes PLANUREX the perfect drive for cable belt conveyors, roller presses, slewing gear units, bucket wheel drives, apron feeders, central drives for tube mills, rotary kilns, travelling gears, agitators and much more. The high torque density of the design allows for very small roller spacing – its low weight reduces the loading on the gear unit and machine. High additional forces from the universal joint shaft and due to the acceleration of the movable rollers are absorbed by the standard bearings. They’re easy to combine with other gear units, e.g. primary helical, worm, bevel or bevel-helical gear units. Low-noise running owing to low rolling and sliding speeds at the tooth flanks. The high overload capacity provides for operational reliability and stabilizes your process, also saving operating expenses owing to high efficiencies and optimised maintenance intervals.
Further information is available at www.siemens.com.
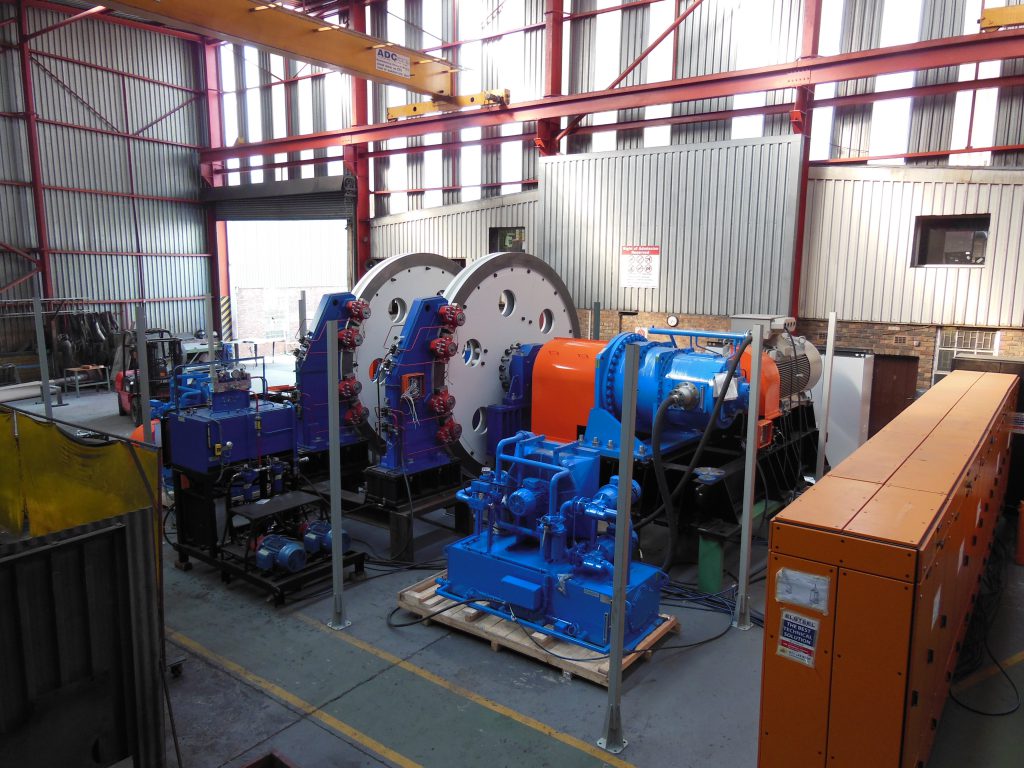