BD Manufacturing PR
Thought Leader Profile: Sewela Ngcobo – CCBSA Midrand Manufacturing Manager
Sewela describes herself as a mother to two beautiful and disciplined children, a 14-year-old son and 9-year-old daughter, and a proud wife. At 38, Sewela is a qualified Industrial Engineer and says that she has always been deliberate about her career path since she was in grade ten. She initially wanted to be a pilot, and her father cautioned her about always being away from home. She then explored Aeronautical Engineer, but opted for Industrial Engineering, which allowed her to spend time in execution and use her analytical skills.
Sewela also describes herself as a deep thinker, highly analytical and very structured – and says that being able to put the analytics and execution together has, over the years, allowed her to realise her full potential.
Let’s take a closer look at Sewela’s journey and how she has shaped her career to what it is today…
Talk to us about your journey
A: I started in 2010 as a Manufacturing Development Specialist Trainee in Midrand, and six months later, promoted to Manufacturing Development Specialist. I came from the automotive background – when you talk about world class manufacturing, the approach is slightly different compared to how we apply the principles in a process or FMCG environment. I remember when I first interviewed for a role with the Coke system, it was a different skill I had, which got me in! My next role was Process Support Manager; I was one of the team members to visit Elgin to fetch the formulation during the commissioning of Appletiser.
I remember walking in there and asking how they make it, and this prompted me to go back and think of a structured way of capturing the process in a factual data standard inclusion. I used an FMEA (failure mode effect analysis) which is a tool to determine the process and steps involved, what could possibly go wrong, and the severity of it happening. It was important that we captured how to make Appletiser and also understand the sensitivity that goes with it. I didn’t have a dedicated project engineer at the time, so I was a part of the whole process while also running operations. I was at work from 2 am to 10 pm every other week.
At this point in her career, Sewela was also a new mother, again to her six-month old daughter, so she had to find a balance between work and taking care of her family. She says that the pressure became too much and, therefore, resigned. But it wasn’t too long until she was back on the job market again…
I was later found by someone who also worked at legacy ABI but had moved to Unilever, and they were starting a new function of industrial performance. I looked after factories in Africa from a capacity utilization. It was a very interesting period for me. I was later promoted to Technology and Regulation/Innovation Manager before another promotion to run the liquids factory as a Manufacturing Manager – you know as they say, the rest is history.
Sewela shares that she later decided to take a break and have a “mom-job”, so she took up a role at Danone as Supplier Planning Manager in January 2020…
They only had one factory which supplies nationally, and it was a couple of months until Covid-19 started. I had never planned a single thing in my entire life (giggles*) – it was, however, interesting because it gave me an exposure and understanding of how the business works from a sales demand perspective (the innovation pipeline) – to translate what sits outside in commercial, and then into tangible cases on the floor. What I enjoyed most, because I had production and operations experience, was being able to understand what is bottom up and creating a plan which aligned with the business plan but also optimal and efficient.
In January 2021, Sewela lost her father to Covid-19 and says that they had a lot of plans. This was a turning point for her as she started to think about whether or not the Supplier Planning Manager position made her feel alive, to which her answer was no because she couldn’t physically and tangibly see the results. Sewela said that she wanted to do work where she could get involved and solve different problems every day. Heading to West Africa, where she was going to be a Supply Chain Manager for one of the top companies, Sewela was asked to return to CCBSA as an Executive Assistant (AE) to Henry Peek in September 2021.
You recently won the Managing Director’s Manufacturing Plant of the Year Award for Nigel. Tell us more about that?
A: When I came back as an EA, I was seconded to Group Office supporting the Project Management for the Integrated Operating Model. I remember at some point saying to my then line manager that I would love to move back to manufacturing upon completing the project and it just so happened that the Manufacturing Manager then was moving to Head Office in a different role, and then I moved to Nigel in her place.
And now you’re back in Midrand, where it all started for you as a Management Trainee, your first experience in the Coca-Cola System. How does it feel to be back?
A: It feels unreal! Being here eleven years ago as a trainee, and if you had told me that I’d be back as a Manufacturing Manager, I would have laughed – and that’s the long and short of it. It’s not because of lack of vision; considering this role and the amount of responsibility and accountability and how big this job is, and looking at the little experience I had then – the leadership capability I was loading, I couldn’t have imagined growing into this type of a leader.
What I admire the most about this role is being a purposeful leader – everything you do and how you touch people’s lives, how you teach the right behaviour to create the right culture is so important. You’re literally almost under the microscope all the time. In everything you do, you have to be a cautious person of your actions and be very deliberate about what you spend your time on, what you spend time teaching people. But also what you spend time appreciating, and letting people know that you appreciate what they do. It’s easy to get lost sometimes and forget that you’re here to work for your team and not that your team works for you.
Our job is to make stock available – the important thing is that the people who are making the product believe that they’re extra ordinary. The same goes for things that are not a part of the culture, you must be deliberate in ensuring that your people know that it’s not allowed and may have consequences.
It’s about creating opportunities for my teams to learn to make decisions as I would, because I also aspire to make choices like my line manager. I want the factory to get to a space where everyone in the team is so good that you cannot tell who the team leader is – they must each be self-directed. One must have a certain level of disciplined thinking and execution. As a leader, I want to challenge people to do things differently – be firm and fair. I find that the most engaged people are the ones challenged every day to do things differently, even if it’s just one thing!
You have spoken about how you want to create a disciplined culture and influence behaviour – creating a self-directed team. What do you see as the must-wins for the Midrand team in 2023?
A: The first one is around how we use water – usage ratios and how we optimise using the borehole because we have access to it. The second one is our energy because it is volume driven so we should be able to understand our phase loading of our volume for us to, not just break-even with our energy utilization but also optimise. It’s the simple things – operators and everyone in the factory to come up with simple, small actions that will have a very big impact on energy and water usage. Another win will be improving our USLEs (factory efficiencies) from 50-60%. And lastly, getting back to the fundamentals post the Covid-19 impact; Covid-19 has interrupted some of the daily routines which will get us to our fullest potential so we must improve our engagement approach i.e. daily team meetings.
How will you support the team to ensure the plant delivers its business goals?
A: I think that what’s important is to create a thinking environment through engagements (two-way communication). I want to help the team to do more than having a discussion if we want to move the needle – I want to drive joint accountability, as a team. Another critical one for me is the visual performance management. For example, if the team spends a week doing problem solving, I then join them on the floor where the problem occurred for individuals to showcase what they have done and how they have resolved the issue. People want to be heard but they also want to show their capabilities, and the best approach is to have a structured problem-solving environment or platform. I find that this creates positive energy for the entire team in general to always want to achieve more than they set out to. In my opinion, Midrand has brilliant people – if I can get everyone to believe that about themselves, I would have won.
What is your approach to leadership (especially as a Manufacturing Manager)?
A: I am a leader that will not give you the answers but challenge you to think until you arrive to the answer. I’m unapologetic about being a demanding leader – I demand more and the best out of people. I’m a leader who clears obstacles and value a real connection than a transactional relationship with people I work with. My team is underpinned by the fundamental to respect, I always want to have functional and respectable relationships. We must be able to take accountability, which I also don’t do very well but push to hold myself accountable and allow my team to hold me accountable – the message delivery must always be done with respect and care, both ways. Taking pride in our work – I want the Midrand team to be proud to invite others to come see their factory and what they do to get it there.
CCBSA recognises its responsibility to use water sustainably, including in manufacturing processes, and its role in helping to improve South Africa’s water security. Talk to us about the plant’s initiatives to save/conserve water; what drastic changes can we expect in managing this resource at the Midrand plant?
A: If everybody gets to a point where they see a dripping tap and they want it fixed immediately, then everyone would be at a point where they understand the importance of water and value it. Some of the small things we can do is not only create awareness, but even with our basins, put taps that have water automation and sensors. Also, how we use our water recovery from clean in process (CIP) and really maximise how we are using the borehole. For us to reach the number one spot this year, we have to change the way we think about things. Let’s prepare for the future today!
What have been some of your biggest wins in your career?
A: At Unilever, I saved 6.5 million euros in reformulation and around 3 million rands in loss reduction, and also won the Purposeful Leader award in 2019. I have done a Section 189 with no strike and no job loss; we found a home for the people reduced in other factories – I remember being at work every morning at 6 am to be present with the teams and to reassure them. The Appletiser commissioning and the Nigel Plant of the year award are also big highlights for me.
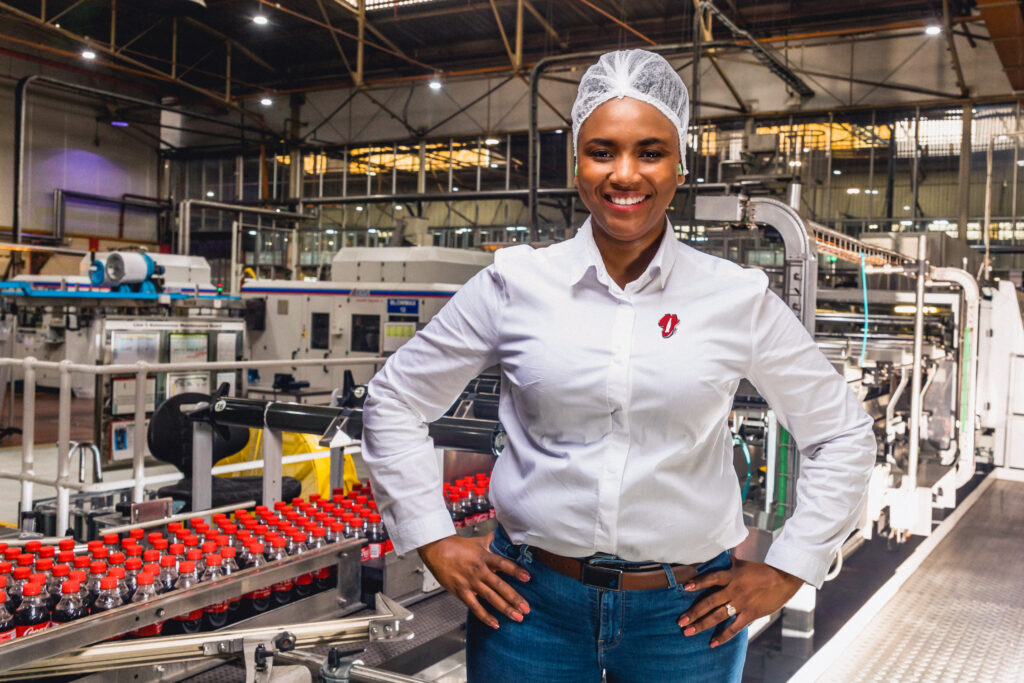