SA Mining
Tech Talk
Iron ore producer Kumba Iron Ore, which has since 2014 embarked on modernising its mines by implementing the best available technologies at its operations, aims to become a leader in the beneficiation of low-grade material, Glen McGavigan tells SA Mining.
According to forecasts issued by Forrester and Gartner, business and government spending on technology goods, software and services will increase by 5.1% this year and 4.7% in 2019. IT spending is anticipated to increase by 4.5% year over year globally in 2018 to $3.7-trillion.
Kumba Iron Ore (KIO), which holds a 73.9% interest in Sishen Iron Ore Company (SIOC), mines the high-grade iron-ore Sishen mine near Kathu in the Northern Cape and Kolomela mine near Postmasburg.
Given that Sishen’s life of mine (LOM) is currently pegged at 13 years, the company is looking to extend the LOM using a two-pronged strategy, beneficiating lower-grade materials and exploration activities on its existing lease.
SIOC has injected R749-million in technology improvements for the period between 2014 and 2017 and allocated an estimated R300m in 2018.
Given that the iron ore producer is looking to leapfrog industry in the beneficiation of low-grade materials, it is too busy with a feasibility study aimed at modifying its existing plants to handle low-grade materials.
“Together with Exxaro, Kumba Iron Ore has developed an ultra-high-density separation technology that enables us to lower our feed grade and allows us to beneficiate lower-grade materials. The project, which involves the conversion of the dense media separation (DMS) plant at Sishen into an ultra-high-density medium separation (UHDMS) plant, is currently at feasibility study stage. It is expected to deliver an additional 2mtpa in production,” says McGavigan.
The Sishen mine has a DMS plant constructed in 1975, JIG plant (2008) and smaller UHDMS plant (2015) that beneficiate the run-off mine material to produce high-grade premium products. The older DMS plant will be converted into UHDMS with full production estimated towards the middle of 2022.
Two-thirds of product from Sishen mine is delivered to the Chinese market while the remainder goes to Japan, Korea and Europe.
Sishen mines high-grade ore which includes 25mm 65% Fe lump (DMS), 25mm 64% Fe lump (JIG plant), 27mm and 20mm 66% Fe lump, and 8mm 64.5% Fe fines. Its lump-to-fine ratio is 60:40.
Technology improves safety and production
KIO’s aggressive technology drive dovetails with its strategy “to be the best in class in the next five years delivering awesome results every year”.
The company has identified a three-horizon strategy, which entails improving business in terms of reducing costs, increasing production and achieving better prices for its high-quality product in Horizon 1, growing its current life of mine beyond the 13 years through exploration in Horizon 2 and investigating potential value-adding opportunities that arise from diversification, beneficiation and consolidation in Horizon 3.
According to Kumba Iron Ore’s CEO Themba Mkhwanazi, the safety initiatives already under way have seen Sishen mine meet the mining industry’s target for a zero fatality rate in 2017.
Safety initiatives include the installation of automatic braking technology on its heavy mining fleet which “detects objects close by and slows equipment accordingly”. “The intention is to roll out the system across all 97 trucks operating at Sishen mine by June 2019. To date, 36 trucks have the technology installed,” says McGavigan.
KIO is also leveraging off disruptive technology by rolling out a real-time condition-based monitoring system, which monitors the health of both plant and equipment.
“Sensors that measure the condition of the plant and equipment in real time will be installed. This means that we will be able to predict equipment failure before it occurs and react accordingly.”
Added to this is the recent installation of a wireless mesh across the entire Sishen operation which supports, for example, the operation of geospatial tools, including drones that are used to gather data.
Apart from safety, productivity improvements of between 30 and 40% have been achieved and “while other factors may also have contributed to the increase in productivity, technology has certainly been an enabler”, notes McGavigan.
At Kolomela, KIO recently introduced an advanced process control (APC) system that reacts “intelligently” to the feed entering the plant. “By changing the settings on the plant, it is able to generate more lump product, which sells at a premium. The introduction of the APC system has resulted in a 6% increase in throughput and a 1% increase in lump-to-fine ratio.”
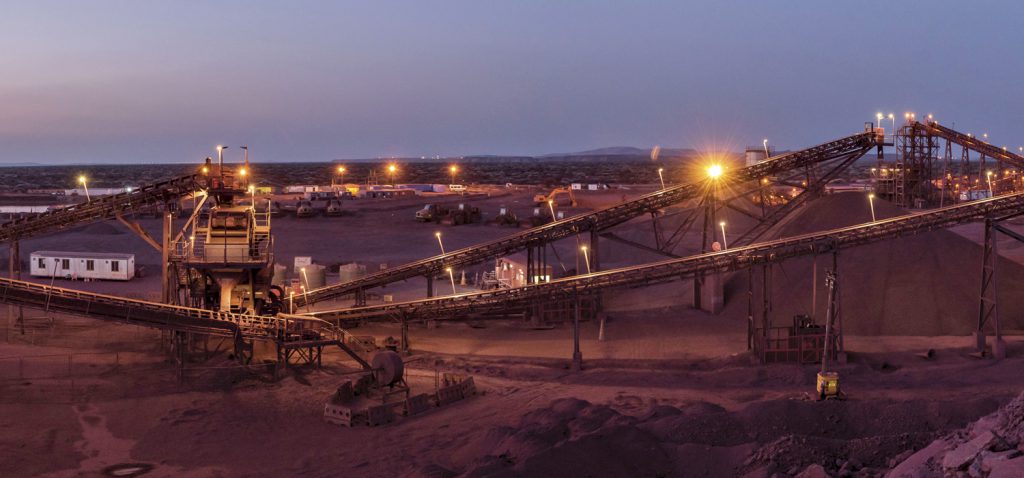