SA Mining
Shaft-Sinking Successes Underpin UMS’s Strong Growth
Underpinning the group’s growth and success is its ongoing work – over three continents – on three major vertical shafts and one decline system. It also continues to be busy with several shaft refurbishment contracts, including on a shaft being sunk for a developing platinum mine in South Africa. In terms of hoisting capacity, the shaft will be one of the biggest in Africa.
“While UMS is much more than a shaft-sinking contractor, as it offers a full spectrum of services that allows it to take projects through from concept to commissioning, there’s no question that shaft sinking is one of our core skills,” says UMS’s CEO Digby Glover. “We are now widely recognised as one of the pre-eminent shaft-sinking specialists globally.”
At Lucara’s Karowe diamond mine in Botswana, UMS is sinking two approximately 750m-deep shafts to enable the mine to transition from open-pit to underground operations. Further afield, it is busy with a nearly 700m-deep ventilation shaft in New Mexico in the United States (in joint venture with an American partner, Harrison Western of Denver) and a 1 500m-deep shaft for a copper mine in Brazil.
New decline system
In South Africa, UMS has been awarded a major five-year contract to develop a decline system for platinum miner Sedibelo Resources.
UMS, of course, is the inheritor of the skills and intellectual property that used to reside within Shaft Sinkers, which over several decades was arguably one of the best and most innovative such organisations in the world. UMS acquired the South African assets of Shaft Sinkers, then in business rescue, together with its design and engineering arm METS, in 2015.
Glover notes that one of UMS’s strengths is its ownership of a fleet of plant and equipment, including a number of hoists that are continually being refurbished and modernised. The fleet would cost more than R2-billion to replace, which is a massive barrier to entry. “Few contractors can match the inventory we have at our disposal,” he says.
The fleet, which includes both new and used equipment, was acquired at competitive prices from several sources. It gives UMS a distinct advantage over its competitors, as hoists in particular are high-cost, long-lead items that can take up to three years to procure.
“The used equipment has been refurbished to the same standard as new equipment by a team of specialists – consisting of technicians and engineers – at our Rand Yard facility in Randfontein, together with various outside companies,” says Glover.
Also contributing to UMS’s success is its deliberate strategy of involving itself in projects as early as possible in the project cycle. This early involvement can shorten project timelines significantly, and also ensures that construction issues are addressed before the start of the construction phase.
Finally, and on the all-important subject of safety, Glover says that UMS has maintained an impeccable record. “Our last lost-time injury was over a year ago, which is a remarkable achievement, given that shaft sinking is a complex and demanding exercise that presents more risks than most other mine development and mining activities,” he says.
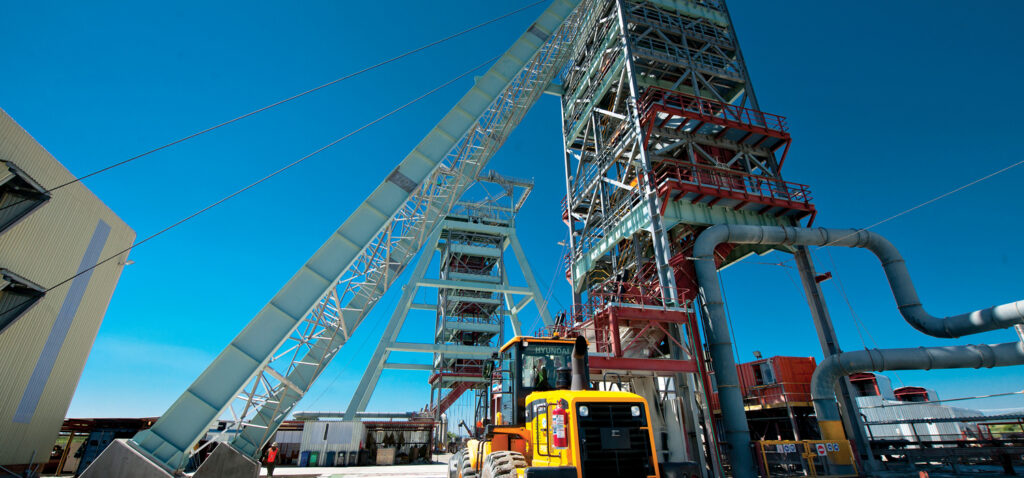