SA Mining
How Mining Benefits From Toll Milling
In the post-mining phase, there is often a need to mill a raw product down into a finer material – something that requires the installation of heavy machinery, along with the expense and skills required to keep it operational. Add to this the time, effort and cost of both the process and of the maintenance required to keep such an outfit operational, and it is easy to see why many organisations seek out a company that can process minerals for them on a toll basis.
According to Andrew Wenger, CEO at African Pegmatite, toll milling services for customers are a very specialised field, requiring heavy machinery like ball mills, roller millers, hammer mills, granulators, dryers, attritors, crushers, screeners and many other pieces of equipment, depending on the material being dealt with at the time.
“There are many parameters to consider when milling,” suggests Wenger, “such as hardness, nature of product, desired output size, input size, abrasiveness of the material, moisture, dry bulk density, along with numerous other factors.
“At African Pegmatite, our focus is specifically on milling virtually any dark material down to size. We mill dark material only – including carbons, irons, chromes, manganese, and certain slags, among others – as our environment is specifically geared towards these darker materials.
He explains that the process of milling materials in large tonnage is not an easy thing to achieve, particularly when it comes to hard substances like the hard slags made of chrome, manganese and vanadium. African Pegmatite has thus positioned itself as a specialist for milling minerals and metals that other organisations would not want to.
“Remember, this is a very heavy industry with a lot of wearing parts, expensive machinery and high electrical costs. It is a process that requires massive machinery, lots of power, and the the know-how and long-term experience to deliver such volumes on a regular basis,” he says.
“Therefore, it should not be surprising to learn that we have a team of maintenance people that is almost as big as the production environment. Their role is to consistently fix, repair and prevent the machines from going down. Since the one thing we cannot do is mitigate wear – as this is essentially our core business – we put the time in to make sure we have the best technology in place to do the job most effectively and consistently.”
Asked about the sustainability of an industry that consumes so much electricity from a coal-based electrical generation system, he notes that the company has now implemented two solar power projects at its plants, with the aim of producing more of its own greener electricity.
“We are pleased with our growth in recent years. The company was originally heavily reliant on a single product, in a single sector, for around 70% of its business. Thanks to the team’s hard work and proactive approach, we now service five core sectors, as well as many new products, with the organisation also exporting to some 44 countries globally.
“How do we differentiate ourselves? At African Pegmatite, we have over half a century of experience in the mineral processing industry and have dealt with some of the hardest materials one can mill. We also have the experience and the machinery to assist businesses with the processing of the required minerals from their raw form, in order to have them ready for the customer to add into another process further downstream,” says Wenger.
For more information, visit: mineralmilling.com.
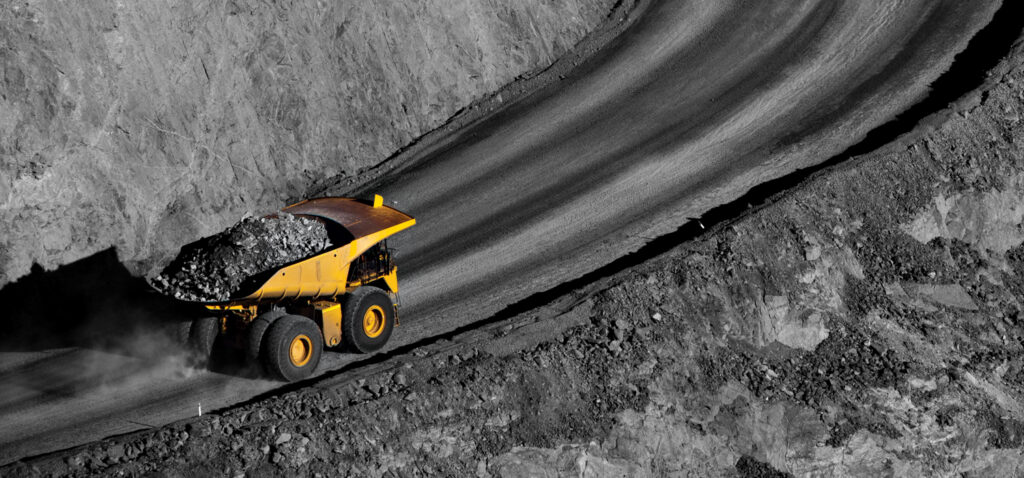