SA Mining
Future Technology Now
By: Nelendhre Moodley
The COVID-19 pandemic has dramatically altered the way we work, live and play – and those whose businesses are constantly evolving in line with changing times are best placed to adjust to the new normal. The pandemic has brought with it a complexity of new challenges, and as such, the entire world will have to adapt to new effective ways of conducting business, says Komatsu Mining Corp Africa’s Benton Bell, marketing and capital sales director.
“Among others, it will impact the availability of funds and perhaps limit the appetite for risk, as there will be much less to go around,” he says.
The mining sector has been under huge pressure due to the fall of commodity prices, and is expected to be severely impacted by recent events.
In April, the International Monetary Fund (IMF) predicted that owing to the pandemic, the global economy was projected to contract by 3% in 2020 – which was much worse than during the 2008/9 financial crisis. According to the IMF’s Gita Gopinath, the cumulative loss to global GDP over 2020 and 2021 from the pandemic could be around $9-trillion, greater than the economies of Japan and Germany combined.
“Even though as Komatsu Mining Corp (KMC) we look at various financial solutions to assist our customers, this is new territory for us and we will have to be as lean and efficient as possible to mitigate the impacts. We need to be placed in the best position now so that we can be much stronger when we return to the new normal,” says Bell.
Innovation and technology
Peter Phahlane, director of product management, notes that the escalating costs of mining coupled with production and safety challenges have pushed the industry to look for solutions that technology can provide.
“It is obvious that advanced mine automation is the next step in the industry – already mining houses and various role players including original equipment manufacturers have set up programmes around the theme of advanced automation.”
To this end, Komatsu has been driving innovation and technology as a business imperative.
The company has invested in a number of different programmes and these have resulted in the development of products and services that help its customers to move towards full automation of their operations.
“We are developing partnerships with our customers to ensure that our research and development (R&D) and their needs are aligned. We believe that the value of advanced automation will be achieved when key challenges facing the customers are resolved through partnership. For instance in our underground coal mining business we are working together with our customers to align our technology roadmaps with their needs. The key to achieving our automation goals does not reside in the development of the technology only (R&D) but also with the art of mastering the implementation of technology. Komatsu utilises both internal expertise and our customers’ expertise through partnerships to realise these goals,” says Phahlane.
In line with advancing its technology drive, the heavy equipment manufacturer has invested a lot in upskilling its employees.
“It is important to note that the interaction between people and technology will be the core of the future mining environment. As such, we have invested in upskilling both our employees and customers’ employees through our upgraded training offering, which has been repackaged and improved on to enhance our training candidate experience. We have introduced advanced technology into our training offering including hologram projectors for 3D experience, Underground Tablets mixed application for ongoing (virtual and e-learning) and on-the-job training, as well as advanced simulators. These developments equip both the mine and our employees with necessary skills and knowledge required to handle advanced technology for now and for the future,” he explains.
Product innovations
Over the past few years the company has launched a number of new products and systems including the latest Joy 12HM37 Continuous Miner range with state-of-the-art control system Faceboss 2.0. This product range is designed to improve safety, productivity and reduce costs. The control system is designed for automation and provides the required platform to develop and deploy automation features through various programmes in partnership with its customers.
The JoyConnect system is suitable for data collection, analysis and actions. The architecture of JoyConnect is designed to handle big data and simplify data/information handling. Manipulation of data has opened up new avenues where new features are developed such as underground haulage mapping. This feature allows for underground equipment’s position to be traced and located in real time similar to how GPS has on surface but without the use of GPS satellites.
Komatsu’s mixed reality application is equipped to handle advanced developments of new technologies. This is a tablet application installed on approved devices that is used to train operators and technical personnel, anywhere, anytime at their own pace. Using both virtual and augmented reality, the application provides the user with real-time audio visuals to illustrate complex technical concepts and simplifies the task at hand. The application also assists technicians in resolving troubleshooting, guiding them during maintenance and assisting operators on safe use of the equipment.
Faceboss – future technology now
“For our underground coal mining business, we have made considerable advancement in terms of our installed bases on our new control systems, Faceboss 2.0. At the moment, we have over 18 Faceboss 2.0-equipped machines operating locally at our customers’ operations – this gives us considerable opportunity to trial new features for automation. We are currently running trials at customers’ mining operations both locally and internationally to research coal visualisation sensors that will assist with real-time section visualisation, machine controls (sump, depth, heading control), autonomous shuttle car, etc. So far we have achieved exceptional results from these trials. Full section automation for underground coal mines are drawing closer day by day. These developments will strengthen our position as a technology leader in providing mining solutions,” says Phahlane.
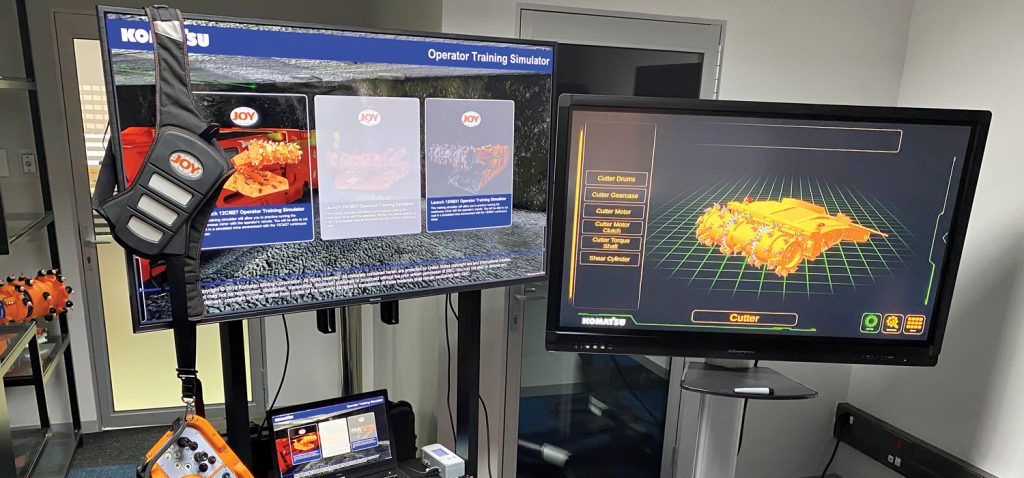