SA Mining
Future-Ready
Canyon Coal has spent over R16-million on skills development over the past five years. This year alone, despite the onset of the pandemic, the company has injected over R3.6m into upskilling its workforce and the communities surrounding its operations.
Its training programmes have resulted in all-around operational improvements ranging from productivity improvements to better health, safety and environmental standards.
Nthabiseng Ocia Mueti, group social labour plan manager at Menar, the private investment company that houses Canyon, says continuous skills development is an inherent part of the company’s strategy.
“We believe that for the mining industry to progress and modernise, it needs to employ more workers who have higher qualifications and enhanced skills to enable the sector to operate more safely and efficiently,” says Mueti.
Upskilling for Industry 4.0
As the mining industry drives modernisation and innovation and advances technology uptake, so too must employees evolve to adapt to the changing needs. Upskilling and training the workforce is imperative as companies adopt new ways of operation, which include elements of artificial intelligence, virtual reality, augmented reality and big data, among others.
According to Mueti, Menar is always evaluating how to integrate the latest technologies into its operations and looking at how best to ensure that the company has sufficiently skilled people to make the best use of these technologies.
The mechanisation of mining is resulting in greater technical knowledge to build, maintain and repair mining machinery and equipment. The depletion of resources means precision mining skills will also become key to the success of mining operations. “Yet there is a shortage of well-trained and experienced artisans to service the growing number of trackless mining machinery (TMM) that is found in modern mines,” says Mueti.
Moreover, existing TMM operators continuously need to be trained and kept abreast of new trends and the latest technological innovations that are being applied to these new advanced technologies in order to correctly operate their machines and limit downtime. Mechanised training programmes provide artisans with specific skills in mechanised engineering that are not part of the traditional training syllabus.
“Sadly though, many graduates remain unemployed after completing their studies, even though they attended respected accredited training centres. This is because in many instances the curriculum did not match the needs of prospective employers, because the training did not include training on the latest technologies being used in the mining industry.
“Overhaul and updating of training programmes are needed as a matter of urgency to address this situation. Modern training needs to include blended methodologies including e-learning, virtual reality, simulation and workshop practical hands-on training to allow trainees to receive comprehensive modern training that is relevant to an increasingly tech-savvy sector.”
Upskilling the community
Upskilling the community at all its operations is important to Menar, and according to Xolile Mankayi, group social licensing manager, skills development and training increases community members’ opportunities of securing a job within the mining sector.
“Menar is committed to offering training courses to community members ranging from basic to advanced levels, in order to build up a comprehensive mining skills database of accredited and trusted people who have received the proper training. To this end we offer a range of training programmes such as articulated dump truck, front end loader, tractor loader backhoe, excavator training, among others, as well as vacation work to our bursary and non-bursary holders,” he adds.
To address the mining skills shortage in the Bronkhorstspruit area where Canyon Coal’s Khanye Colliery is located, Canyon Coal embarked on an upskilling programme for locals, which included training 20 community members on mobile machinery for surface mining, Hazchem firefighting and first aid training over a 30-day programme.
The company also runs regular adult basic education training (ABET) programmes at its mines.
Between 2018 and 2019, nine groups of 15 people were trained from Level 1 to Level 4 (NQF 1) in numeracy and literacy at the Phalanndwa Colliery ABET Centre in Mpumalanga. Since its establishment in 2015, over 60 people have been upskilled through ABET programmes run at the mine. This year the company is embarking on an operator skills programme to re-skill qualifying members of its host communities in Phalanndwa.
Youth and women development
Aside from actively recruiting female mineworkers, machine operators and engineers, among others, Menar strongly supports female equipment and service providers throughout and is especially focused on the empowerment of women in local communities.
“Increased recruitment of women in mining is good for enhancing the sector’s diversity. Diversity means strength for the sector. It’s good for operational sustainability and improved overall performance as diverse teams make better decisions.
“At Canyon Coal (as of the end of September 2021), we had 76 female employees accounting for 26% of our workforce, with 29 in core mining positions and 21 in mining support services positions. Canyon Coal prioritises key and core career opportunities in mining for females, such as operators of articulated dump trucks, excavators, dozers and graders, among others,” says Mankayi.
He says the company has numerous examples of success stories of individuals who started off as bursary recipients and now are department heads in the company.
“For instance, at just 29 years old Nthabiseng Mueti was appointed SLP manager on 1 October 2020. She was able to attain both a Diploma in Mining Engineering and a Blasting Certificate through the help of the bursary and internship she received from Canyon Coal.”
Training success stories
Examples of training success stories at Menar include, among others, Jabulani Jiyane who started as a cleaner at Canyon Coal’s Phalanndwa Colliery in Delmas. He advanced his career through Canyon Coal’s skills development initiatives, undertaking a number of the training programmes, and subsequently climbed the ranks at the company. Most recently he was promoted to the position of blaster at Khanye Colliery in Bronkhorstspruit.
“I am very appreciative of everything that Canyon Coal has done for me. I hope to continue to grow and learn new things and be part of Canyon Coal’s story of growth and development for many years to come,” says Jiyane.
Another success story is that of Zwivhuya Phathela, 30, a mechanical engineering intern at Khanye Colliery who says, “as part of attaining a Government Certificate of Competency (GCC) to become a certified engineer, one needs to be exposed to both the electrical and mechanical aspects of engineering”. Therefore she has received training on electrical aspects of the mine, such as how to connect the wires in the plant, and service motors and lights.
“Phathela is currently being mentored by Khanye Colliery engineering foreman Brian Gwaze, and is exposed to heavy earthmoving machinery and the importance of adhering to the Mine Health and Safety Act,” says Mankayi.
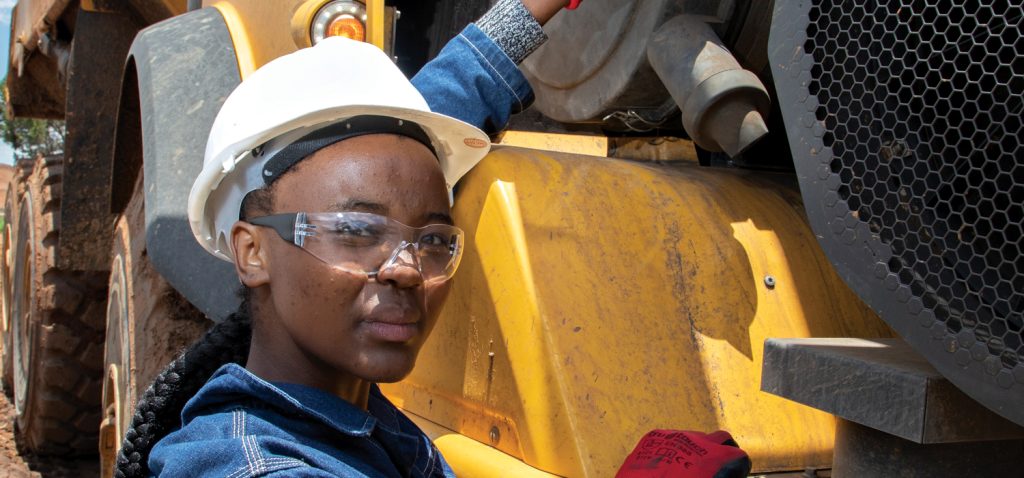