SA Mining
Electric vs Diesel-Powered Pumps
Few people question the wisdom of using diesel-powered pumps, particularly for temporary sites or rental arrangements. Their faith is well-placed: diesel-powered portable pumps have been the standard for decades, supported by diesel’s high and reliable power output and low energy costs.
Yet, while diesel remains a strong option, electric pumps have become a viable alternative, even for temporary and rental use cases. In terms of overall cost and value, electrical pumps are a compelling alternative, and where projects consider environmental and carbon-reduction factors, it’s a leading choice.
Since both types of pump offer different benefits, and come with different challenges, it is worth comparing the two options, to determine when – and under what circumstances – mines should consider implementing either diesel or electric pumps.
Projects suitable for diesel pumps
Chetan Mistry, strategy and marketing manager at Xylem Africa, says that diesel pumps suit three main use cases: no electricity, incredibly heavy-duty workloads, and short-term projects.
“In most cases, the best scenario relates to at least two conditions. For example, if a site lacks electricity, it can still use alternatives such as solar power. However, if the project duration is short, the upfront cost of solar installation or installing a grid connection might not be economical, leaving diesel as the preferred option,” he states.
“The typical recommendation is that if the pumps are required for three months or less, diesel is more economical, and if the duration is longer than three months, electrical power starts becoming more economical.”
Diesel pumps, continues Mistry, are also incredibly hardy and can handle heavy workloads, specifically meaning liquids with large solids or high viscosity. While there are comparable electric pumps that also handle such workloads, the typical conditions where you find such liquids are usually temporary and in hard-to-reach areas.
Drilling down even further, Rob Bond, area mining manager for KSB South Africa, points out that there are two specific types of projects where diesel tends to be more effective thasn electric.
“Realistically, if you are going to make use of diesel pumps in a mining project, the most important areas to implement these is in pit dewatering units, while diesel is also highly recommended for firefighting units,” he says.
Where electric pumps are most suitable
“As for electric pumps, they can most effectively be utilised in projects related to hard rock, industrial minerals, dredging, and diamond mining applications,” continues Bond.
Mistry notes that diesel pumps have earned a reputation for being hardy and portable, which often makes electric pumps seem inferior. However, modern electric pumps are as capable of heavy-duty jobs and often have lower maintenance requirements.
“The main distinction today is access to power. If a pump site can access electric power, via a grid, solar, or through heavy equipment such as drilling rigs, and the operating duration is more than three months, electric pumps become the more economical choice.
“Any site needing permanent pump installations gains more from electric pumps, which can run on the main grid or a solar installation. Basically, if it makes sense to invest upfront for long-term pump sites, then electrical options are more predictable and cost-effective than diesel options. Electric pumps are also much quieter than diesel pumps, and tend to require less maintenance.”
However, it’s not responsible to simply declare that one type of pump works best for a given scenario, he adds. Modern pumps have more in common than ever before, such as supporting heavy-duty workloads or requiring less maintenance. The right pump depends primarily on a site’s requirements. Designing a pumping plan for a site will get better results than following a preference for a specific type of pump.
Deciding on a pump
Mistry explains that mines have many pumping requirements: dewatering, dust suppression, fire suppression, water recycling, filtering tailings, and human consumption, to name a few.
“There was a time when you could clearly divide the jobs between diesel and electric pumps, but modern pumps provide more versatility – especially with the advent of solar-powered pumps. Thus, a site’s needs are far more important than the choice of pumps. To put it differently, you first need to know what pumping jobs you want to address, before deciding what kind of pump you need,” he adds.
“Take underground drill sites as an example. Drilling uses water to cool equipment, suppress dust, and remove loose sediment. The water pools under the drilling area and must be removed through dewatering. Traditionally, this was the domain of diesel pumps, because they can be moved into the dewatering area. In contrast, electric pumps were more cumbersome and required power cables that increased electrocution risks.”
However, he indicates, new-generation electric dewatering pumps can be installed onto the drilling rig to use the rig’s power, and the operator can manage the pump from the cabin, thus removing mobility and electrocution concerns. In such circumstances, using electric dewatering pumps becomes more economical.
KSB’s Bond adds that diesel units are suitable where there is no power available, and are also effective for back up if there are power failures, allowing operations to continue.
“Diesel units are perfectly suited for mobile operations. Electrical units, however, are more efficient, cause less harm to the environment, and have the capability of running at higher speeds to get more head and flow. Meanwhile, electric units are less complex and can be driven directly using variable frequency drives (VFD), which also improve the efficiency and reduce power consumption,” he says.
Challenges to overcome
“Diesel units are limited to the operating head and flow, due to the limited speed a diesel engine can run at. Diesel units also have a severe impact on the environment, due to the fuel emissions.”
Electric units, he suggests, require a lot of power, so an ongoing challenge like load shedding impacts on their operation. Here, a mine might instead turn to diesel, even though this uses excessive fuel and escalates costs.
Mistry agrees, stating that if a site lacks electrical power, diesel is the better choice. However, running those motors often costs much more in maintenance and fuel, especially if projects last longer than three months.
“The key to success is to put in the time and effort to design a pumping plan suited to the site. It may make sense to run rental diesel pumps for the short term and install electric pumps for permanent operations. It may be cheaper to have a diesel dewatering pump on the back of a bakkie, or it could be better to have an electric dewatering pump that can run remotely for months, because it requires less frequent maintenance,” he says.
“Ultimately, you shouldn’t throw pumps at your problems. Rather, decide what those problems are, and then work with pump experts to design a pumping solution that meets your short- and long-term requirements,” he concludes.
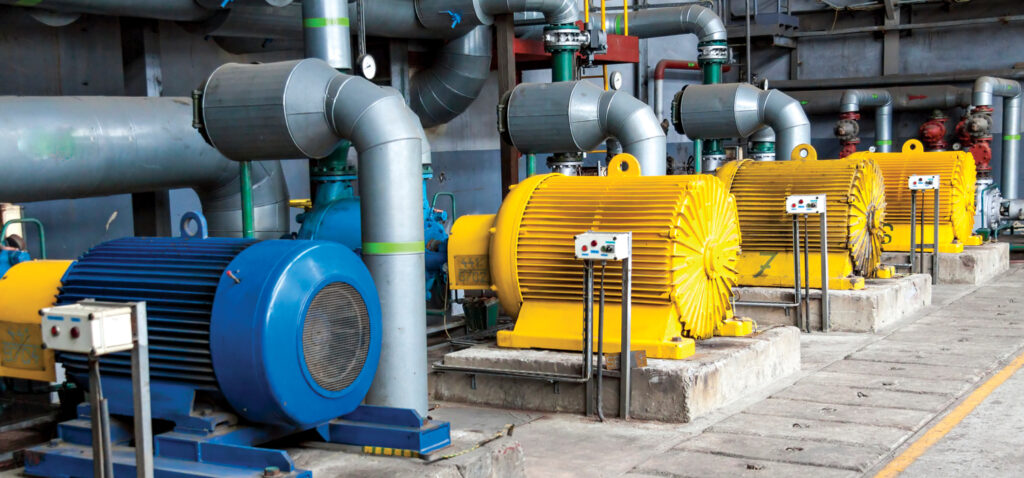