SA Mining
Can Phosphate Mining Be Done Sustainably?
Phosphate mining is considered essential for global agriculture and the role it plays in food security. Like many mineral extraction processes, responsible production and manufacturing processes are vital to mitigate potential environmental damage and ensure a safe working environment.
These activities are governed by strict legislation, and a range of regulations designed to protect human health and safety, biodiversity, and to limit the extent of any polluting contaminants.
Mark Maynard, COO at Kropz, notes that at the company’s Elandsfontein mine, environmental and safety mitigation measures are engineered into its design and were implemented at the inception phase.
“At Elandsfontein, our focus has been on minimising habitat destruction; maximising land reclamation; responsible management of water resources and intensifying wastewater treatment; reducing chemical usage; and – through a focus on R&D – developing cleaner extraction and processing technologies,” he says.
To this end, Elandsfontein employs a full-time rehabilitation team, whose activities are closely aligned with the mine’s environmental management programme (EMPR).
Adelaide Ruiters, founder and CEO at Adelaide Ruiters Mining and Exploration, which is developing the Zandheuvel Phosphate Mine and Beneficiation Plant in Saldanha Bay, points out that many phosphates contain high levels of cadmium, which is illegal in SA.
Cadmium levels of more than 20 ppm may not be imported or used for agriculture production in SA, since cadmium is a toxic heavy metal that causes kidney and cardiovascular diseases, as well as cancer.
“The phosphates we produce are among those that have very low cadmium content, making them much healthier. However, the biggest problem in SA is that around 70% of our phosphates are actually imported. Are there any assurances that imports like these, and their cadmium levels, are being properly policed at the ports?
“Ultimately, we must remember that price is often key in this market, so the imports coming from elsewhere may be cheap, but there is every likelihood they are also high in cadmium.”
It is for this reason, among others, that she indicates she is trying to form a Phosphate Producers Association to lobby other producers to advocate for both healthier phosphates and phosphate mining approaches. It would also be to ensure that South African phosphates are used in the South African agriculture value chain.
Water issues
In a water-stressed country like South Africa, explains Ruiters, a strict focus on water management and efficiency measures is clearly appropriate.
She notes that tailings dams are broadly at odds with the principles of sustainability, which is why her company uses filter presses to remove the water, so that it can be circulated back into the process.
“It’s worth mentioning that beneficiating phosphate rock concentrate allows you to produce phosphoric acid, which is a key element in producing fertiliser and other agents, like dishwashing liquid. It can even be further beneficiated as a food chain preservative, and can be used in items like soap and toothpaste,” she says.
“However, when such beneficiation is undertaken – through Direct Froth Flotation Technology – diesel is usually used as the frothing agent. Because of the carbon footprint this creates, we have replaced diesel with a canola oil derivative, which is far more sustainable and assists significantly in producing low carbon footprint phosphates.”
Ruiters adds that SA’s water scarcity issues mean that it is not really sustainable to use potable water in the beneficiation process. Therefore, her company has forged an arrangement with the local municipality, which allows them to utilise treated municipal wastewater instead.
“In the end, our beneficiation process has been made more sustainable in three ways. Firstly, we replaced the frother diesel with canola; then the fatty acid traditionally used in the process is now also derived as a byproduct of canola production; and finally, we replaced caustic soda with potassium hydroxide, which allows us to produce a greener, more sustainable low carbon phosphate fertiliser product, targeting more sustainable organic agriculture practices.
“We also designed a pipeline to pump our final product to the logistics facility at the Saldanha Bay deep sea port. In this way, we eliminated the need to have trucks transporting the product to the harbour, mitigating the dust and air pollution a mining operations causes.”
Technology to the rescue
According to Grant Dreyer, MD for Future Metals and Materials at Afrimat, technology can also be embraced throughout the value chain.
“From the identification of economically accessible resources, through to mine scheduling, monitoring and processing, and on to data analytics to help ensure compliance, technology offers plenty to the sector. Included in this is its ability to assist in the overall reduction of environmental and safety risks.
“These tools, together with a firm commitment to regulations, enable planning that helps to optimise mining and production processes, while reducing emissions, safety risks and other environmental impacts,” he explains.
Kropz’s Maynard points out that by integrating these modern, digital technologies into the overall mining planning and operation, organisations can significantly improve many aspects of the mining process.
“However, there are a few caveats. Improving your business using technology relies on observing practices and disciplines such as sound investment in research and development (R&D), collaborating closely with technology providers, as well as collaboration between mining companies and regulatory bodies. It is also imperative to ensure that the workforce is trained to use the digital tools.”
Digital technology plays a key role in managing sustainable mining initiatives and reducing a mine’s environmental risk profile, he continues. Elandsfontein, for example, has bespoke training programmes in place to keep employees skilled in the latest developments in this area, in order to benefit from these new innovations.
“Sustainable phosphate mining relies on an integrated collaborative approach, involving all the industry stakeholders – government at local, provincial and national level, NGOs, communities and others. Ultimately, it is important to balance the need for phosphates, which is critical for food security, with responsible environmental stewardship, to minimise any potential ecological damage,” says Maynard.
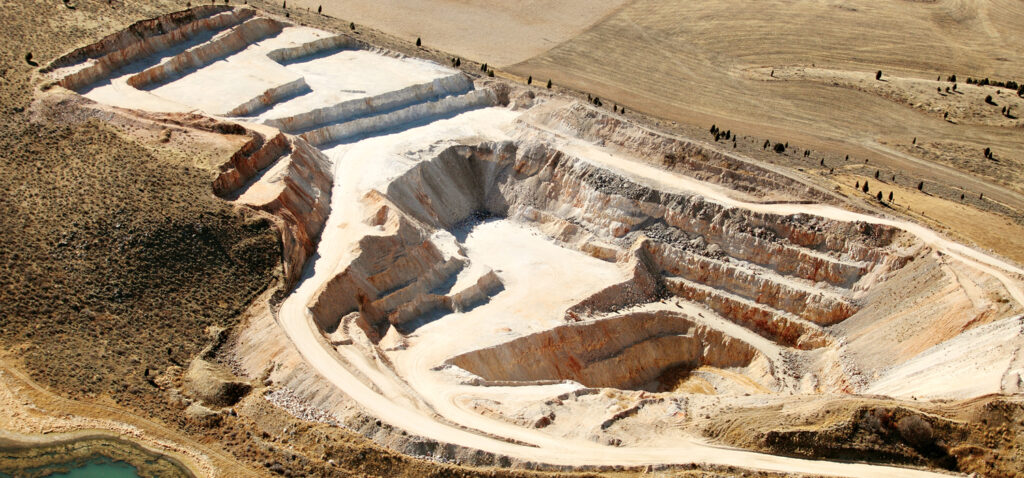