SA Mining PR
ANDRITZ Water Management For Responsible Closure Of Mines
At the end of 2018, the centuries-old tradition of mining hard coal in Germany came irrevocably to an end when the last remaining collieries were closed down. Following years of debate, a joint decision was taken by politicians, industry and the trade unions in 2007 to close down all mines. This is because German coal can only be mined under extremely difficult conditions and only from extreme depths. In order to compensate for the impact that this effort has on the price, state subsidies are needed if German coal is to be able to compete on the market at all.
However the term “closure” in connection with mines sometimes conveys the wrong impression because the mines are far from being at a standstill just because actual mining work has come to an end. On the contrary, the operators are responsible for ensuring that the mines are cared for and maintained in the long term in a process that is, above all, sustainable. This includes socially compatible personnel adjustments, but also rehabilitation of former mining areas, repairing and rendering safe any mining damage, and responsible water management.
Long-term mine water concept
The latter, in particular, is one of the most crucial, eternal missions – work that will be needed long after the year 2018. Systematic water management has so far dealt primarily with ensuring that the effects of industrial mining don’t cause pit water to enter mines that are still active. This is no longer needed after a mine has been closed. When mining work stops, the main concern is to ensure that the mine water doesn’t mix with the groundwater above it. Mine water is rainwater that seeps into the ground and solubilises various salts and minerals from the layers of soil on its way through them. Due to this absorption of minerals, any contact with the layers containing drinking water must be avoided at all costs.
The mining company RAG plans to let the mine water rise to a point where there is still a safety margin between the mine water and the drinking and groundwater. To do this, RAG will have to pump around
110 million cubic metres of mine water. This is a challenge that can only be overcome with expert knowledge, a powerful team of 300 specialists, the latest technology, and high financial commitment. RAG currently expects annual costs of over €100-million.
In the course of the historical shift of mining operations in Germany to the northern part of the country, a largely continuous network of mine workings was created. These connected mines made it possible to combine the pump locations of disused mines to form so-called water provinces after closure of the last pits. Thus the mine water can be pumped centrally from a depth of around 600m at several combined water drainage locations. RAG is currently collecting the mine water from the mines still operating at 13 water drainage locations. When hard coal mining comes to an end, only six of these original mine water drainage locations are to remain.
Two solutions are better than one
Implementation of this concept to resolve the problem of mine water in the long term places very high demands on the manufacturers of suitable pump technology. Pumping large volumes of liquid from great depths generates very heavy loads. Up to 30 tonnes of axial thrust are produced and have to be eliminated. The answer: two solutions are better than one. A design with a double-suction submersible motor pump can fully compensate for the axial thrust.
At the moment there are very few manufacturers on the market who can supply this special pump technology needed by RAG, and there is only one that also has the necessary references and operating experience: ANDRITZ.
The pumps expert for mine water
International technology group ANDRITZ produces and supplies double-suction submersible motor pumps through its subsidiary ANDRITZ Ritz GmbH, with headquarters in Schwäbisch Gmünd, Germany. These are multi-stage, double-suction submersible motor pumps that can fully compensate for the axial thrust and have 50% less flow speed. The economic advantages are maximum operating reliability, minimum wear, and an extremely long lifetime of more than 20 years. Every pump with heavy-duty mining (HDM) technology is customised from standard modules for the specific application in hand. Hundreds of these pumps – including the largest submersible motor pump in the world at over 22m long – are operating successfully all around the world, for example in the most important mines in China or South Africa.
For the RAG project in Germany, pump specialist ANDRITZ will manufacture and deliver a total of three double-suction submersible motor pumps like those for the South African project based on the patented HDM technology, which has proved its worth several times over. With a weight of 13 200kg, the pumps are placed freely in the shaft underneath the shrouding tube. At a speed of 1 470 revolutions per minute, these hydraulic machines achieve an efficiency of 81% and convey 530m3 of water per hour from the depths of the former mine over a head of 830m. In order to achieve the necessary capacity, each of these submersible motor pumps is equipped with a special water-filled, high-voltage submersible motor. This motor provides efficiencies of 91.5% and a rated capacity of 1 750 kilowatts. These are four-pole motors as they are much more robust than two-pole designs. As a result of the longer lifecycle this provides and the lower wear, these motors guarantee significantly higher operating reliability – indispensable for this particular application.
Additionally, over 1 000m of cable were laid for operation and monitoring of the pumps. While a thick, 5KV cable provides a reliable supply of electricity to the motor, a manometer ensures that each pump always has the necessary counter-pressure to start up. Furthermore, the temperature of the motor is controlled by means of platinum sensors. The danger from methane gas is monitored by measuring hoses in the shrouding tubes. When the drinking water well goes into operation, one pump conveys the mine water first, and a second pump may be added if necessary. The third pump is available as standby. With this overall concept, the technology is excellently suited to begin reliable and sustainable operation in the long term.
ANDRITZ stands for passion, partnership, perspectives and versatility – core values to which the company is committed. The listed group is headquartered in Graz, Austria. With almost 170 years of experience, around 28 400 employees, and more than 280 locations in over 40 countries worldwide, ANDRITZ is a reliable and competent partner and helps its customers to achieve their corporate and sustainability goals.
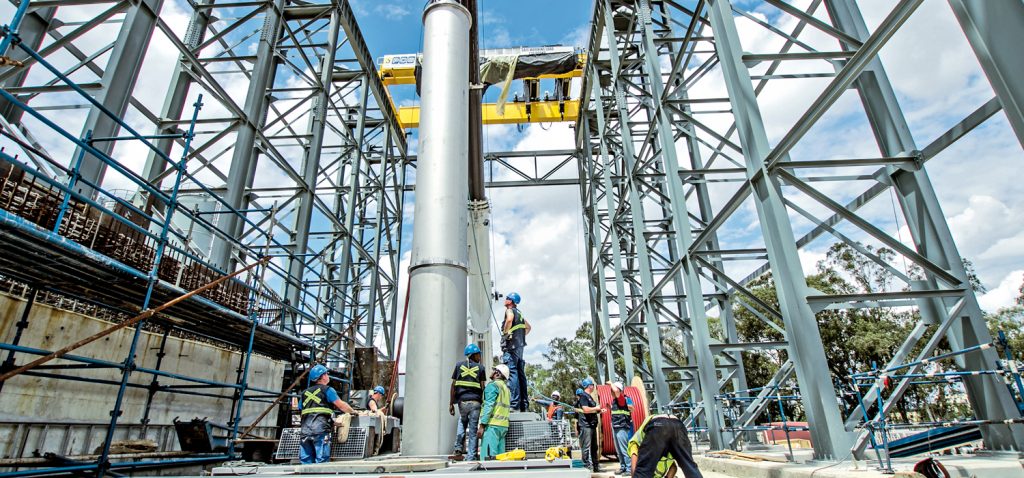