Rock Surf & Deep
The Reel Problem With Grinders
Grinders are becoming a bit of an issue – on a competitive level and increasingly also in social angling. The big problem is when they get submerged, or even just dipped in the sea, serious problems are starting to happen. It’s getting to the point where some folks are looking at them now as little more than a consumable item – yet they aren’t selling at consumable prices.
Unique to our local surf fisheries in Southern Africa, we wade out through shallow waters to then cast into deeper waters, and here lies the problem – the reels get submerged and despite all
the efforts of the various manufacturers to get somewhere close to making them waterproof, they all pretty much fail – miserably.
The problem is that fast reciprocating shaft running with all sorts of seals and gaskets. The water will get in – end of story. The slightest wear on the seals in the lovely mixture of salt water, silt and sand will then transfer salt water down through the one-way bearing, the main bearing, and hence into the gearbox of the reel. And this is where the real problems start.
Because designers have gone to all the trouble of multiple layers of seals and gaskets, hoping to avoid saltwater ingress, they have opted for using soft metals for the gears – like aluminium or zinc oxide. These then start to corrode, as the salt water can’t get out – because of all the seals and gaskets. Once this corrosion starts to have an effect, then either reciprocation mechanisms or the gears themselves start to jam, fail or in some instances strip teeth. Then comes the very expensive exercise of getting scarce spare parts for these reels, if they are even available, and often they are not.
The problem is potentially deeper than just the materials the designers are choosing to use, as anglers are looking for smoother, stronger and greater performing reels, as well as lightness. These expectations, which are admirable in most instances, are the root cause of the failure of many of our more modern reels. By reducing the weight of most of the moving parts, the reels inevitably become lighter, and with the addition of multiple bearings at friction points, they also become smoother.
However, for lighter parts for mechanisms, “less heavy” materials like aluminium are used. Whether it is forged, machined or cast, it is still aluminium, and has a propensity to corrode when in contact with salt and water. Sure, there are some grades of aluminium that are less prone to corrosion, but they are expensive and more difficult to work into gears and reciprocating mechanisms.
Added to the corrosion problems are anglers’ desire for stronger grinders that can withstand ever-increasing drag loads, because of the strengths of the braids we can now use. Stronger drags are being designed into the reels with successive models, but at the end of the day, all this does is transfer even more load onto the teeth in the main gear, which is usually a soft metal. This then exacerbates the avenue of failure.
Back when we were all fishing with multipliers, we would never have considered any reel that had aluminium components other than side plates. Gears were always either marine-grade brass or stainless steel, and despite years of abuse, we never had any problems apart from the occasional replacement of bearings, which really was a simple task.
Recently I dug through a storage box of old tackle, and found a grinder that had been retired from active duty, as it was now over 25 years old. The reel was a Penn Spinfisher, built back in the days when Penn was still an American company, and built its reels there. Out of curiosity I opened it up to see how it was inside, and to my amazement it still had grease on the gears, and absolutely no corrosion. However, what was even more significant was the size of the gears and bearings in this reel – huge and all made of marine brass and stainless steel.
The reel when originally bought had been slightly upgraded to carbon drag washers, as I had used it in northern Angola for cubera snapper, jack crevalle and tarpon – with nylon. It was surprisingly not far below the drag strengths of the reels that we have today. Heavy? Yes, very, and probably not the most distance-casting machine ever built – but more than adequate to handle big fish and sharks.
The point here is perhaps that 25 years ago we could buy fixed-spool reels that were very robust in construction, and more than adequate in design to withstand the abusive nature of our fishery, yet we are mostly unable to buy anything that approaches such a standard of design and durability today. There are a few out there, but you do have to look hard to find them, and not all of them come with a five-figure price tag. There are some very nice “exotic” standard reels about with all the attributes our current reels are missing – but they tend to be seriously expensive.
A worldwide search found some well-designed distance-casting reels, but their weaknesses in construction put them in the same field of problems that we have with models currently available through local importers. However what was apparent was the large number of models that we never get to see that are extremely specialised in design for maximum casting distance. Tall tapered or parallel spools with awesome line-laying mechanisms that put lines on the reel, like they were laid by a precision machine. Reels built with pure ease of distance-casting in mind. But despite these huge benefits to be found from more European market reels, there would be problems with durability, especially when wading.
Unfortunately the big main players in the reel market are basically selling us hype, with exotic-sounding names. The point is that a lot of the advertised information sounds very impressive, but what is more important is what is not written. Below is a small caption from a well-known and popular reel manufacturer, from their sea spinning reels section, and a model that is popular in Southern Africa.
– DFD: Precision Dual Force Drag system
– Multi-disc, Japanese oiled felt drag system
– 4HPB + 1RB corrosion-resistant stainless steel ball bearings
– Quick-Set anti-reverse roller bearing
– Precision machine cut brass pinion gear
– HDGII: Corrosion-resistant, High Density gearing
– ALC: Rigid diecast aluminum frame and sideplate
– Precision Elliptical Gearing system
– Custom blue anodized machined aluminum handle knob
– EVA handle knob on
– Hydro Block water tight drag seal
– RESII: Computer balanced Rotor Equalizing System
From a quick read it sounds superb, but why would you part with R2 500-R3 000 of your hard-earned cash?
First, “felt drag” washers are very suspect, and we would all hope to get at least carbon fibre drag washers these days, and not have to try to get after-market replacements. “4HPB +1RB” bearings sounds a little too few to be a realistic long-term product, and probably has a number of nylon bushes to compensate, eight bearings might be an absolute minimum for a good smooth running reel. “Precision Elliptical Gearing system”, great – it’s made of aluminium?
The hype mentions a brass pinion gear, great – but what it doesn’t mention is the material for the main gear. Which, when you finally get the cover plates off, is made of cast aluminium, with small teeth. Oh! That was the “HDGII: Corrosion-resistant, High Density gearing”; forgive my cynicism, but high-density cast aluminium is resistant to corrosion for perhaps a couple of hours in salt water, and then it starts a terminal chemical reaction that will weaken or eventually dissolve the small teeth on the main gear – the one that is doing all the high-pressure work.
Last, the “Hydro Block water tight drag seal”, which doesn’t mean that it is “waterproof”. But then you wouldn’t need “Hydro Block” if the drag washers weren’t cheap and inexpensive water-susceptible felt.
This advert was taken at random, and is not meant to be specifically focused on that company, but it is fairly representative of the sort of information, or lack of accurate information, that is being promoted. There are numerous examples within the covers of many publications, and it is a sorry state that the industry is in currently.
In closing, the story isn’t one of total gloom and doom, as there are some very fine products out there, and not all have a five-figure price tag. Personally, I have been using a Quantum Cabo for the past four years in all sorts of fishing situations, and to date it hasn’t had a single spare part. Yes, it does get opened up after every trip where I have been wading, to get the water out of the “gearbox”, but it has never let me down. The newer Penn Spinfisher Long Casts do have stainless steel main gears, and a water-sealing system that fails, but against the odd drop of water that does get in, it won’t wreak havoc when it gets trapped in there. The common theme of both these reels is that they are surprisingly easy to access the gearbox, just four or five screws and the side cover comes off for easy maintenance.
Sometimes the “good old days” were good! Tight lines everyone.
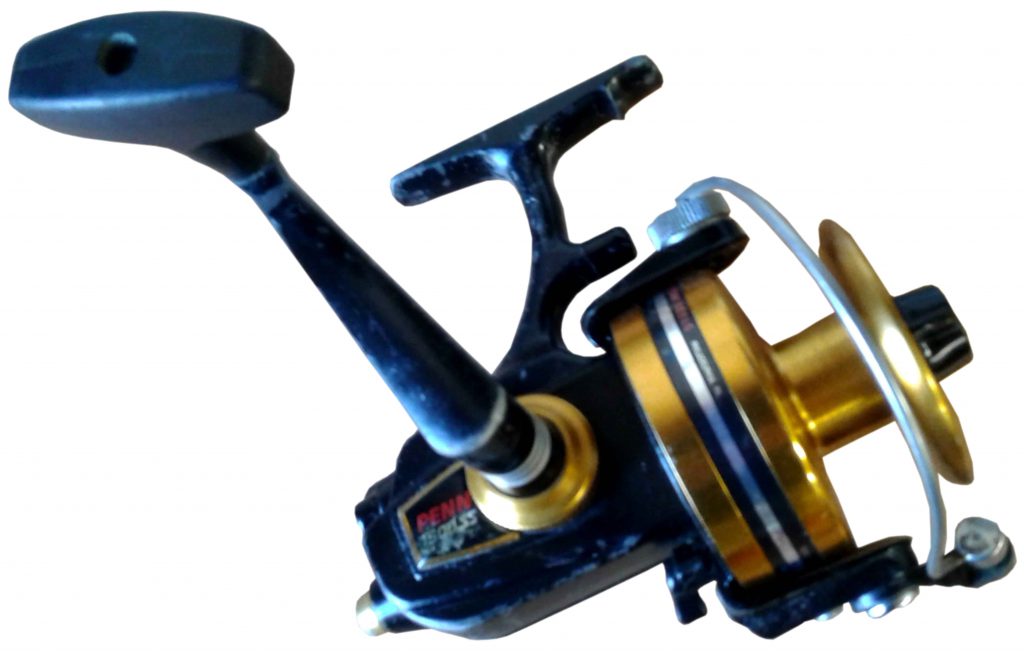