Business Day Commercial Property
The Evolution Of Commercial Warehouse Design
The JJL 2018 Trade Trends report shows South Africa to be a significant net importer, stimulating demand for new warehousing and distribution centres that are close to transport nodes.
For this reason, design criteria for warehousing and distribution facilities have evolved, with considerations such as green building technologies and energy efficiency also influencing design.
Shoprite’s Award-Winning Distribution Centre
Shoprite’s Cilmor Distribution Centre, located off the R300 in Cape Town’s northern suburbs, comprises more than twenty buildings, the largest of which are three warehouses serving as the core of the development. The biggest is the
76 000m2dry goods warehouse, followed by the 18 000m2refrigerated building and the 12 000m2returns centre.
Niel Marx, a director of Cape Town-based firm Steyn LeRoux Truter Architects, is the lead architect on this mega project, which earned first place in the Southern African Institute of Steel Construction’s Steel Awards 2018 in both the warehousing and roofing/cladding categories. Referring to the technologies used on site, Marx says: “The building uses long span steel frame roof structures, allowing substantial storage and manoeuvring space below, in line with emerging needs for large maxi units. Major emphasis was on fast but safe construction methods, using innovative technologies to deliver a light failure-tolerant structure. The buildings are stabilised by large cantilevering concrete tilt-up columns that were constructed during the fabrication period of the steel. The largest of these columns was 24.3m tall, weighing more than 44 tons.”
Environmental considerations were also important. “Gone are the days of ugly sawtooth industrial roof designs. The client did not want its distribution centre to be an eyesore, so aesthetics was a core part of our brief. The park can be seen from the freeway and surrounding communities, so we proposed a design concept that would be aesthetically pleasing and fit with the shape of the silhouetted Tygerberg hills forming the northern backdrop. Environmentally, there is much more under the roof. For example, to increase energy efficiency, the smoke extraction vents in the roof also let in the natural light, reducing usage of electrical lighting,” he adds.
Global Technologies In KZN
In KwaZulu-Natal, well over R1.9-billion had been spent by 2018 in developing the massive Clairwood Logistics Park.
Nico Prinsloo is the development manager for Fortress REIT Limited, a JSE-listed property real estate investment trust, which develops its own properties. They began work on the state-of-the-art R4.5-billion Clairwood Logistics Park in 2012 and have now completed about 25 per cent of the overall project. Prinsloo says that the project will take at least four years to roll out to full completion. He says that leading international engineering technologies that are a first for South Africa are being employed underground.
The first 25 000m2warehouse at the park has been completed and handed over to the tenant. “This comprises a 24 000m2warehouse plus an office block on the southern side. The warehouse measures 13.5m to the eaves, providing for high stacking that appealed to the tenant who was looking for substantial storage space. It was designed with logistics companies and freight forwarders, who needed to split and reload bulk cargoes for redistribution, in mind,” says Prinsloo.
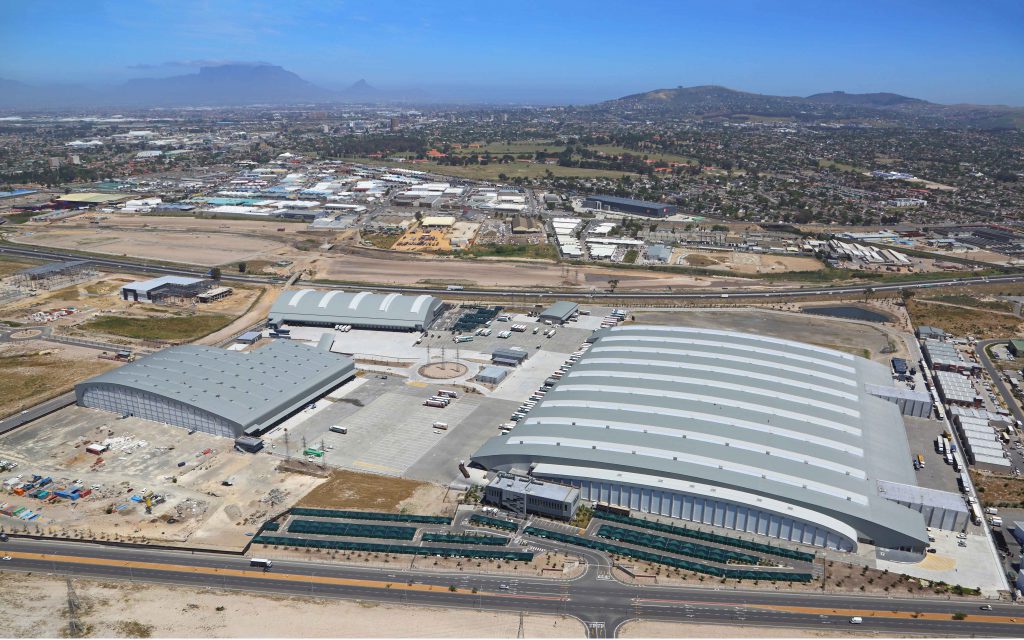