BD Manufacturing
PPE Demand Causes Industry Shake-up
South Africa has wide manufacturing capabilities, however, these vary substantially between products based on complexity and access to technology, equipment and skills. “Some items like face masks for public use are relatively easy to produce, while others such as gloves require more specialised equipment and materials,” says Shakeel Meer, divisional executive for manufacturing at the Industrial Development Corporation. “When the COVID-19 pandemic hit, some companies facing temporary shutdown switched to producing essential and personal protective equipment (PPE) products,” says Meer. “Automotive manufacturers started producing face shields and other companies redirected products to new uses, for example, potable-alcohol producers supplying alcohol for sanitisers.”
Switching an entire factory to producing new products is a complex process. “Local businesses quickly had to identify and source the required materials, design the products, retrain their staff and build expertise,” says Meer. “They also had to meet quality and safety standards.”
Because different standards apply to different products, prospective manufacturers need to do careful research. “Items classified as medical devices require licensing by the South African Health Products Regulatory Authority,” says Meer. “Bodies like the National Regulator for Compulsory Specifications also set standards for PPE and there may be guidelines set by government departments or specific buyers.”
Keeping prices down
At first, insufficient local capacity to supply PPE was exacerbated by global shortages that made imports difficult. Some companies took advantage and charged a premium. “Keeping prices down requires sufficient supply to meet demand together with competition in the market,” says Meer. “Economies of scale may be important: some products can only be produced competitively if they are manufactured in sufficient volumes. We learned that countries and manufacturers tend to give preference to supplying their local needs first. Local manufacturing capacity can, therefore, be important not only in keeping prices down, but also ensuring that critical PPE is available at all.”
These boots were made for walking:
BOVA
“BOVA, the leading safety footwear brand, provides 550 direct and hundreds of indirect jobs,” says senior brand manager Vanessa Ronald. “Most components are sourced locally, but sometimes local capabilities or technologies are not available or commercially viable, like safety toecaps.”
To compete with imports, BOVA creates boots that protect wearers against specific hazards. “We focus on the right protection at the right price – safety is our top priority,” says Ronald. “In 2019, we launched our dual compound rubber range, making us the only company in Africa that can produce this highly technical boot.
“The opening of the market to imports at the beginning of the ‘90s decimated our local market, leaving thousands unemployed,” says Ronald. “We have a responsibility not to lose even more jobs; government has worked hard to assure a future for the local manufacturing industry.”
Wayne
BBF Safety, producers of Wayne gumboots, also promotes supporting local. “Around
65 per cent of all raw materials for our gumboots, are sourced locally,” says marketing manager Deane Nothard. “Recycling is important to us: we recycle around 200 tonnes of PVC monthly, sourced from small businesses that collect recyclable material and from big mining companies that supply old products, including gumboots.”
The gumboot market is dominated by local manufacturers. “Gumboots are bulky and heavy, making transport and duty costs too high for imports to compete, especially with the consistent quality of local manufacture,” says Nothard. “To compete, we constantly innovate and invest in facilities, products and people.”
The typical safety standard for footwear is ISO 20345. More technical footwear must also comply with additional standards. “Due to our strong export presence, we also adhere to CE (Europe), Australian and New Zealand standards and accreditations,” says Nothard.
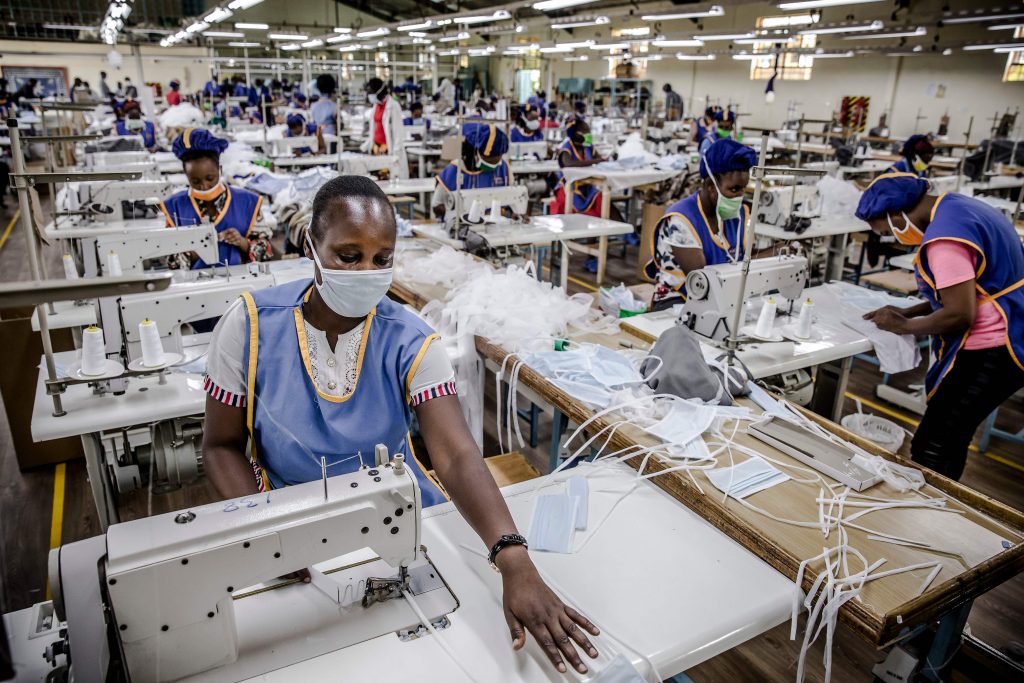