SA Mining
Leveraging Technology To Improve Capital Equipment Profitability
Technology has always been key to mines’ ability to achieve greater loads and, ultimately, returns. This is as true of capital equipment technologies as it is for any other aspect of the mining game.
Not only does technology help to make a dangerous industry safer, suggests Peter Phahlane, product management director at Komatsu, but applied correctly, it improves both productivity and profitability.
“At Komatsu, we have always believed in the benefits of having connected equipment. For example, our JoyConnect offering has enabled us to improve our ongoing digitalisation drive to cover all our underground equipment,” he says.
“The JoyConnect solution is well supported by processes and systems that help to ensure that information is converted effectively into actions that assist customers with key issues, such as high equipment availability and production. We have also developed automation features such as continuous miner automation (CMA) and cutter distance control.”
Phahlane says CMA ensures that the cutting cycle is optimised, as it eliminates human factor deficiency, while also ensuring consistency in the cutting cycle. This results in consistent production and better roof and floor control in coal mining sections.
“We also plan to launch a new product range for continuous miners, along with a new product range, known as Bunker Bolter. These new products will hit the ground this year and we expect these new additions to our range to assist our customers to attain higher levels of productivity in what can only be described as challenging mining conditions.”
Business improvements
Asked how the specific new equipment technologies Komatsu supplies help customers improve their business, he points out that the company works closely with its customers, and the broader coal mining industry, to commercialise technologies like its air mover.
“The air mover solution plays a key role in efforts to reduce the dust exposure experienced by underground employees. We have also developed a screenless scrubber, designed to minimise the maintenance of the scrubber system, once again helping to drive down the underground dust count.
“We understand that investing in capital equipment is a costly exercise, which is why we continuously work on improving the cost of our products. To this end, we have various technology offerings on different equipment, to help ensure that we are able to assist customers with these costs.”
He says Komatsu has also worked on reducing the cost of its rebuilt equipment, in order to ensure that the company is able to offer customers a deal that is aligned to their business strategy, and meets their desire to lower both capital and operating costs.
“One of the key benefits customers gain from using Komatsu equipment is that we have a strong presence in South Africa. Komatsu manufactures most of its products locally, with the local content of its shuttle car and continuous miners (CMs) sitting at over 70%,” he says.
“Another aspect of our service that appeals is the fact that our team of engineers will work directly with a customer, in order to develop a solution that addresses their organisation’s unique challenges.”
He says it’s a similar scenario with Komatsu’s well-developed and trained service team, which works directly with customers on a daily basis, to ensure they are able to obtain the greatest value from both the company’s products and its services.
“In fact, the direct model we use in our underground mining business ensures that we are as close as possible to our customer, and thus able to offer a premium level of service – this is definitely one of our strongest points,” says Phahlane.
The people element
Understanding how best to use the equipment, and to get the best out of it, is also key for the customer, he suggests, which is why Komatsu places great emphasis on training and education.
“We have therefore invested significantly in training programmes, with a view to making sure that they are impactful and assist in uplifting the skills of operators and artisans. We have even developed a mixed reality application for mobile devices, designed to be used by artisans underground, to assist with fault finding and proper maintenance efforts.”
In addition, he indicates that Komatsu has designed a mobile vehicle – installed with hi-tech equipment – that can actually take training directly to the mine’s site.
“This vehicle has a satellite that is linked to our smart service centre, along with hi-tech simulators that are used for the purposes of training. The ability to provide onsite training at the mine further improves productivity, and we have witnessed the impact this training programme has had in respect of improving machine availability and increasing production.”
Asked what the future holds for Komatsu and its customers in this sector, Phahlane says the company will continue to support the coal industry with new technologies and solutions, designed to improve mining capabilities – until the last coal is mined.
“We have plans in the near future to introduce new offerings that will assist the industry with other challenges it faces, and will also soon be introducing a new range of CMs. Moving forward, we will continue to not only launch new technologies and solutions, but will remain focused on assisting our customers to drive costs down, and to ensure that the clients’ total cost of ownership for our equipment delivers genuine business value.”
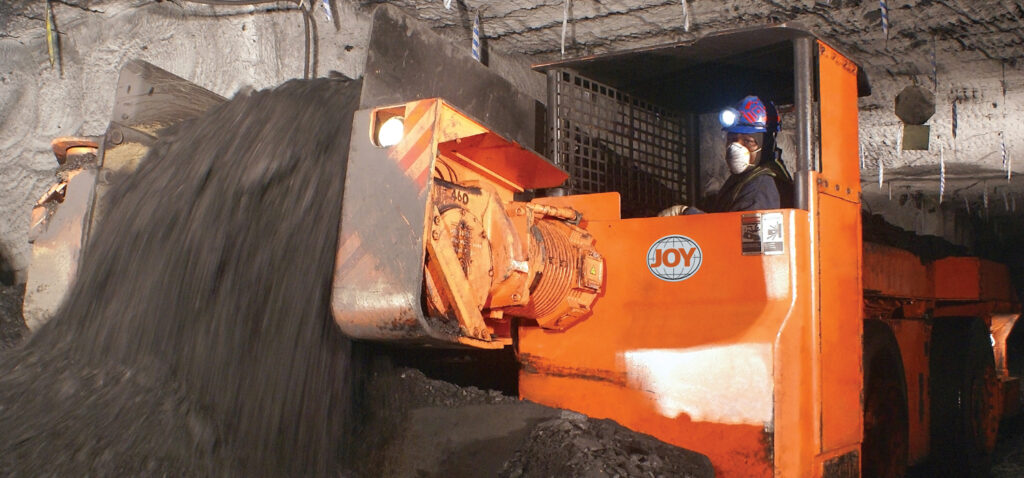