SA Mining
Better Safe Than Sorry
By Rodney Weidemann
Technology, and the innovation that drives it, offers enormous benefits to the mining industry in the way it can be leveraged to improve safety across the sector.
This encompasses everything from safety training to solutions for on-the-job safety, and even includes using technology to help in handling the risks involved in the post-mining closure phase.
Leveraging technology
The latest technological advances in training, in the form of virtual reality (VR), are being introduced locally by KBC Health & Safety. Innovation manager Natalie Pitout explains that using VR allows learners to experience a simulated version of real-life dangerous scenarios. In this way, they can safely learn to mitigate the associated risks.
“The benefit of simulation is that it is not a real-life situation where a possible fatality could result. Instead, any wrong actions can be addressed safely and proactively,” says Pitout. She adds that VR is not a standalone competency module, but is being introduced as part of a blended learning approach.
Blended learning means there is a theoretical component designed to impart the necessary knowledge, which learners are then assessed on, followed by a virtual reality experiential component by means of headset goggles.
“A major benefit of virtual reality is that we can put people from different industries together in one room with the same virtual setting,” she says. “For example, coal and platinum miners can be engaged together to identify common hazards in their respective segments, and we can actually see how different workers react in different situations.”
By introducing analytics on the back end, she says, it becomes possible to identify if people are making the same mistakes, or whether they are identifying similar risks.
“If people are seen to be making the same mistakes, the hazards or risks can be identified for clients, and an appropriate virtual reality simulation suggested to remedy that problem.”
Wearable solutions
When it comes to the safety of mine workers, says Thando Sibindi, managing executive for Mining, Manufacturing and Utilities at Vodacom Business, the company has developed smart technology known as the “connected worker”. This involves a smart device based on narrow band technology, which doesn’t draw a lot of power and can provide longer battery life.
“This device can be worn on the wrist or on their workwear, and as the employee moves around the mine, it sends back real-time information on what is going on in their environment. This allows for reactions in real time.
“For example, if they enter a geo-fenced area they are not supposed to be in, the device will instantly alert them to that fact. At the same time, of course, the operations centre undertaking the monitoring is also able to track that they are in a hazardous zone,” he says.
“The beauty of technology like this is that it not only improves safety, but also boosts efficiencies. For example, we have installed mobile private networks delivering high connectivity and low latency, to enhance the operation of these devices, which has the added benefit of improving communications too. Naturally, workers may be concerned that such monitoring is intrusive, but this simply requires worker education so they understand that this is for their safety.”
A practical example of how it improves safety, he adds, is how – with increasing automation of large mining vehicles occurring – people on the ground are equipped with sensors so that the computer driving the vehicle is aware of where all personnel are at all times.
“Personally, I think that mining organisations are reaching a tipping point as far as digital technologies go. It is critical to stay on top of technologies like this, as they roll out. Wearables like this are a great first step, but mines really need to consider digital transformation and automation as well. After all, the more safety-focused technologies you have in place, the more easily they can adhere to the principles of zero harm,” says Sibindi.
Safety after closure
Ettiene Van Der Watt, regional director of Axis Communications, a provider of internet of things (IoT) solutions, points out that when it comes to decommissioning a mine, there is legislation to be followed around issues of safety and public health.
“Often mines are re-established as grazing land or forest, and sometimes even for residential development. The public health and safety laws speak to the power of off-site monitoring – technology that can be the eyes and ears of the customer, even when no one is onsite,” he says.
“The use of motion detection, cameras and IoT sensors allows the customer to monitor the site, check for movement in certain classified zones, and even grant access rights to relevant individuals – via facial recognition technology – during the decommissioning phase.”
From a security perspective, he says, monitoring starts with security for those high-value autonomous vehicles that can take time to remove from the site. It then shifts to watching for illegal activities onsite during decommissioning.
He notes that in the closure phase, Axis recommends thermal sensors, which can cover tremendous distances, and don’t require lights to do their job.
“These devices can pick up heat signatures and are useful in multiple ways. They can identify accidental trespassers so they can be alerted to possible danger, but can also be used to track and monitor how well wildlife is returning to a decommissioned area, for example.
“The mining industry’s rich history also carries some important lessons, and one of these is that poor closure or abandonment of mines by the industry is a global challenge. It is thus imperative that companies evaluate the risks involved and invest in safety and security measures in the post-mining closure rehabilitation phase.
“Video surveillance systems that are designed to monitor a site with a high level of activity and thermal-based intrusion protection technology are some of the best tools available for securing vast remote perimeters,” he says.
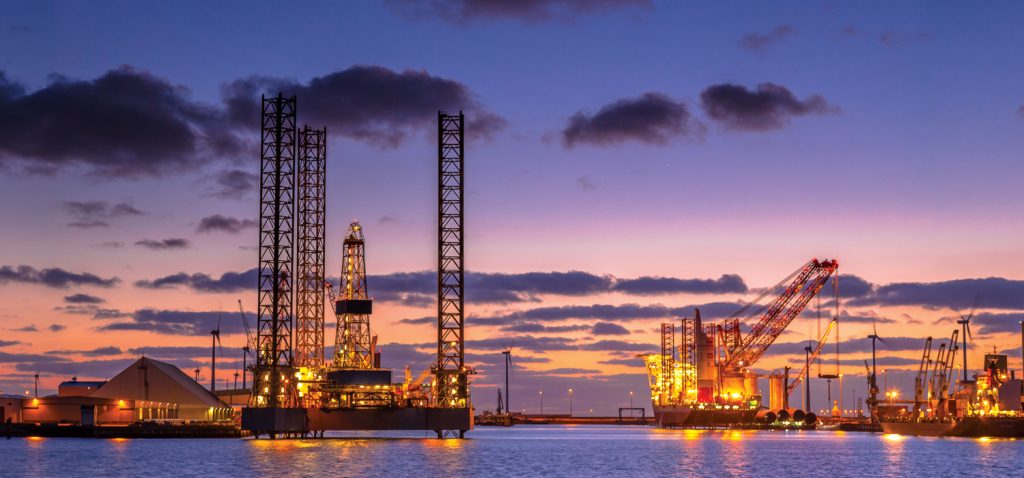