Sunday Times Skills
What Does The Future Hold For Jobs In Mining?
An Australian and an Englishman walked up a kopje. For George Harrison and George Walker, it was a lazy Sunday afternoon when they struck gold atop the Witwatersrand (Ridge of White Waters). Their find happened to be part of a 56km stretch of the richest goldfield in the world.
And so the story began: A ramshackle mining town grew to become the City of Gold. It grew so fast that in just three years, in 1889, the Witwatersrand accounted for a quarter of the world’s gold production, as historians noted. Mining launched South Africa’s economy, and for over 100 years, was the largest contributor to our exports, peaking at 21% of gross domestic product (GDP) in 1980.
Today, mining contributes only 8% of South Africa’s GDP (Stats SA), and 5% of jobs. Performance over the last decade has arguably been abysmal – even during the world’s commodity boom from 2001 to 2008, our mining industry shrank by 1% per year, according to an assessment by the National Development Plan. This is compared to an average growth of 5% per annum in the top 20 mining exporting countries.
Speakers at last year’s Junior Mining Indaba noted that global investment houses put South Africa in the same category as countries such as South Sudan. PwC’s 9th edition of SA Mine, pointed to some improvement in 2017, with revenue increasing by 13% (R43-billion) from the prior year. But this has mostly to do with global recovery in commodity prices helping to bring the industry as a whole back into profitability.
“It’s notable that this is the first substantial increase in more than five years,” says Andries Rossouw, PwC Assurance Partner. Despite layoffs, those still employed are earning more than ever before, according to a recent report by the Institute of Race Relations (IRR) on the ‘Impact of Mining on the South African Economy and Living Standards’. In terms of the mining sector’s profits, employees take the lion’s share at 40%. Mine wages have risen by 45%, far greater than any other sector with mine workers earning almost double the new minimum wage of R20 per hour.
But our high labour cost (up to 60% of expenditure) is making investment less attractive when compared to markets such as the United States and Australia where labour costs average around 30 – 40%. Our labour costs are attributed to the deep level of mining, but are also no doubt due to social and political pressures.
Modernisation for sustainability
Mining houses are therefore turning to mechanisation and automation. “As mining depths increase and conditions become more challenging, the need to modernise the industry is critical,” says Charmane Russell, spokesperson for the Minerals Council. The Council’s approach in this regard is focused on people-centred modernisation. “The development of employees is critical for the sustainability of mining. Semi-skilled work will remain important for as long as deep level mining continues using the current drilling, blasting and cleaning methods. However, the trend is towards more highly-skilled work,” says Russell.
“It’s important to note that modernisation is not simply mechanisation or automation, it’s a process of transitioning and transforming the mining industry of yesteryear,” he continues, “Modernisation could save around 200 000 jobs by 2030, affecting two million dependants.”
What’s more, every miner has about 10 dependants, and for each miner who’s retrenched, job opportunities are lost in downstream businesses. Altogether, the industry supports about 15 million people, according to the Council.
“Despite the misconception that modernisation will replace jobs, increased mechanisation could bring down costs and make mining in SA more globally competitive, allowing mining operations to expand and employ more people,” agrees Dr Anthea Jeffery, head of policy research at the Institute of Race Relations (IRR).
Therefore, skills development is important for the industry at all levels with a focus on literacy and numeracy, technical artisan skills, and graduate programmes in metallurgical disciplines.
John Kane-Berman, Chief Executive of the IRR, notes that South Africa has a long history of skills development in mining. “We have operated some of the deepest mines in the world, including AngloGold Ashanti’s Mponeng, which is five times as deep as the Burj Khalifa, the world’s tallest building, is high. “Finding gold at these levels in the first place, sinking shafts, cooling rock faces, lowering thousands of men below the surface, and hauling thousands of tonnes of rock to the surface is a feat of enormous human ingenuity,” Kane-Berman says. But he points out that this makes mechanisation difficult to achieve. “Almost 80% of the gold mining industry’s output still comes from workers who use hand drills in narrow tunnels.”
Progress is underway. Gold Fields CEO Nick Holland stated in a New York symposium in 2015, that the potential of driverless trucks underground is two to three years away. Anglo American’s Tony O’Neill also announced, at a recent conference in London, that they’re investing in computerised drills with chiselling ability as good as a human’s.
“South Africa may be slipping in other ranks, but the continuing development of mining technology is helping to keep us in the top rank in that field,” says Kane-Berman.
South Africa still has an extraordinary mineral endowment, estimated at around US$2.5-trillion (Department of Mineral Resources). We need to attract investment if we are to grow the industry and boost employment and skills development. Only this can lead to long-term wealth creation.
As Dr Jeffery says: “It is the government that is responsible for creating a policy environment that attracts investment, increases growth, and helps to generate jobs in all sectors of the economy.”
Mining’s most wanted
The Mining Qualifications Authority has compiled a list of 167 occupations in mining that it describes as “scarce skills”. This includes dumptruck drivers and blasters, as well as highly- skilled occupations in policy and planning and geology.
Did you know?
A low-grade mine with a current life expectancy of four years could extend operations to 15 years using semi-mechanised methods.
(Source: The Mineral Council of SA).
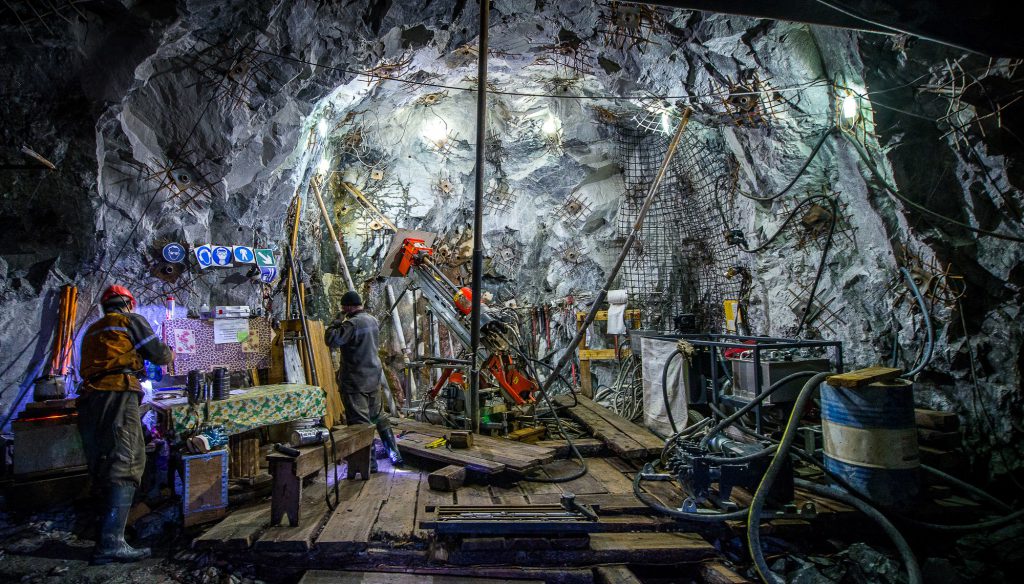