Business Day Safety Safety and Security
How The IoT Is Making The Workplace Safer
As recent tragedies have shown, many South African workers have jobs that must be performed in extreme, dangerous environments – such as mining or construction. Sometimes things go wrong, with awful consequences for the people involved, and workplace safety is always top of mind for regulators and employers.
On top of the risks of death and injury, there’s a financial element to workplace safety that’s often overlooked too. The International Labour Organisation (ILO) estimates that work-related injuries cost the global economy in the region of $1.25-trillion annually.
Can technology provide an answer? There are many who think so.
The Internet of Things (IoT) revolution that is currently under way provides new ways of monitoring and analysing systems in real time. IoT devices are generally described as low-cost sensors that can be networked together, and are best known as the plethora of smart devices aimed at consumers, and intelligence in supply chains, manufacturing and even traffic lights.
One application which is becoming more apparent, however, is that they can provide employers with tangible new ways of prioritising, managing and optimising safety in their businesses.
The key to IoT devices is not just in the sensors themselves. It’s the fact that they are able to gather data which can be aggregated from many places and provide actionable insights in real time. Sometimes, they can be used to remove workers from hazardous situations altogether – drones are becoming particularly popular for monitoring blasting areas, for example. Other times they can be used as early-warning systems to lead workers to safety.
Today’s sensors can accurately monitor temperature, vibration, humidity, and so on, or detect the presence of specific gases or the structural integrity of mine shafts, or other environmental conditions. For workers, heart-rate monitors similar to exercise bands can keep an eye on their vital signs.
When viewed in isolation, the data presented by these sensors doesn’t mean much, but when examined together and interpreted by additional intelligence, it can add up to significant insights. For instance, the ambient temperature of a job site, when considered in tandem with elevated employee body temperatures and increased heart rates, can indicate imminent heat stroke or exhaustion/fatigue.
In the mines
In a report commissioned by satellite communications firm Inmarsat, researchers from Vanson Bourne found that very few mining companies around the world had deployed IoT strategies to date – but within the next 18 months, at least 40% plan to do so. Health and safety was cited as the primary benefactor of IoT, ahead of reducing operating costs.
“Mines are a uniquely specialised, hazardous environment and, as such, miners are highly focused on employee safety,” explains Inmarsat’s director of mining, Joe Carr. “IoT solutions can play a significant role by remotely monitoring conditions and gathering data to anticipate and react to potential safety threats.”
Given South Africa’s vibrant tech industry and the importance of mining, it’s unsurprising to find that there are several local pioneers in the field. Centurion-based IOT.nxt, for example, recently received around R100-million in backing from international investors, largely thanks to its work in mines.
Technology and manufacturing group Ansys Limited is also focusing efforts in the field.
“We have IoT systems for mines that can detect various underground gases,” explains Ansys’s CEO, Teddy Daka. “We also have an anti-collision system for vehicles. Underground it’s dark, dusty and noisy, so drivers have screens that show what’s happening within their vehicle’s perimeter. Miners and vehicles are both outfitted with sensors, alerting drivers and miners about imminent collisions with flashing lights and beeps.”
Daka says the data gleaned from such systems isn’t just used to avoid accidents, but also speeds up investigations when things go wrong or there are near-misses. “We can figure out what happened, and why.” With that knowledge, operating procedures can be constantly improved.
Worker adoption
The important thing is that high-tech systems are constantly in use and vigilant, whereas traditional health and safety training can be quickly forgotten. According to the ILO, employer negligence continues to be a problem, but there are also safety issues around employee habits, which are hard to change. Like the passenger briefing before an aeroplane takes off, safety warnings and best practice are sometimes ignored or forgotten on a personal level, even if they offer life-saving benefits. “Workers don’t feel threatened by these new Internet of Things systems we’re developing,” Daka says. “It’s not intrusive, and they know it’s not there to take their jobs away; instead, it’s there to improve their working conditions by keeping them safe from harm.”
As Inmarsat’s Carr puts it: “IoT technology provides the digital nerve system for a network of automated devices and sensors that adjust to environmental conditions in real time, meaning that equipment can react to potentially hazardous physical changes onsite rapidly without the need for human intervention, removing staff from potentially dangerous environments.”
A manufacturing boost
Just as IoT technologies are emerging as a key way to help mining companies to look after their workers and boost productivity, so they could also aid South African manufacturing.
Many of the same principles apply: by deploying sensors and connecting them to centralised intelligence, factories can get a live overview of what is going on at any given moment, and adjust accordingly. This will boost efficiencies, keep workers safe, and ultimately improve the productivity of the sector.
IoT is not a silver-bullet solution to every industry’s problems, but it can go a long way towards making sure workers are safe, the dangers posed by hazardous work environments are managed and mitigated, and management is aware of workplace conditions at all times.
When deployed intelligently and used proactively, the IoT offers businesses exactly what they need in the 21st Century: real-time insight into their operations, with which to make better business decisions on everything from worker safety to operational efficiencies.
International inspiration
There are plenty of groundbreaking examples of IoT use in mines overseas, too. Canada-based BESTECH offers mine-wide ventilation control systems that save money on energy costs and look out for the health of miners. Data collected by embedded environmental sensors tells the control system where ventilation is needed, shutting it off where personnel or equipment aren’t present and ensuring it’s on where they are, or where dangerous levels of environmental toxins are detected. In Western Australia, the Rio Tinto mining company has deployed driverless trucks in two of its biggest mines, Yandicoogina and Nammuldi, and is now transporting all extracted iron ore using these autonomous vehicles. The argument is that driverless vehicles should be less accident prone than those crewed by humans, and also reduces driver exposure to hazardous conditions. They’re also arguably better for the bottom line, driving efficiencies in mines.
Fast fact
Essar, an India-based international steel company, has saved 5% on maintenance and 10% on fuel costs by outfitting its 3 700-vehicle fleet with an IoT-based tracking and monitoring system.
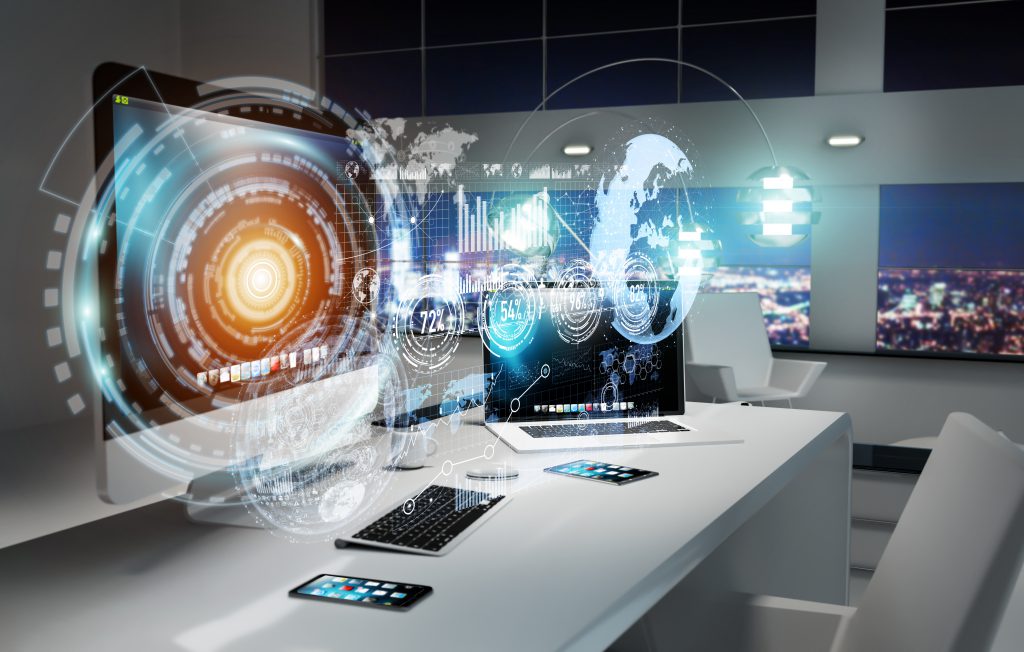