Freight, Logistics and Warehousing
Innovative Solutions To Complex Problems
With its ever-increasing demand for intelligent supply-chain management solutions, the logistics and transport industry has been a key driver behind the Internet of Things (IoT) upswing. Moreover, when compared with many other IoT use cases, “intelligent” logistics operations typically show a faster return on investment while also doing a remarkable job of reducing the core management complexities and associated costs that are top of mind for many companies.
Neil Gouveia, Africa sales manager at Zebra Technologies, points out that complying with government regulations in the transport and logistics industry can quickly translate into a sizeable block of time that drivers must spend on paperwork, instead of actually driving.
“By equipping drivers with a mobile computer, you can create an application that allows them simply to log on to a mobile device, to activate the automatic capture of everything from hours of service to mileage for fuel tax computations, with no further driver action required,” says Gouveia.
“Then, when performing safety inspections, drivers can complete an electronic list of checkboxes, ensuring that inspections are always performed consistently. An unalterable stamp with the time, date and location of the safety inspection can be automatically appended to the form, providing proof that inspections were performed when and where they were required.”
That internet thing
Technological progress is so fast and irreversible, suggests Gouveia, that it can seem threatening to many companies. Nonetheless, digitisation and the IoT hold enormous potential, and if companies don’t want to fall behind, they need to act decisively. Ultimately, he says, a connected, “intelligent” enterprise that connects the physical with the digital world can only increase productivity, efficiency, growth and innovation.
“When it comes to delivering superior customer service, having the right route person or technician in the right place at the right time and with the right equipment is fundamental,” says Gouveia. “Mobile devices alone have impacted service providers by providing a tool to better enable their service position as brand ambassador to the end customer. Now, as the IoT continues to expand, it is becoming a critical component, especially with regards to field mobility.
“With connected devices and IoT technologies, field personnel can gain actionable insights that enable them to interact and communicate better. For example, they can be more proactive by responding to traffic and weather conditions. This not only increases their safety, but also allows them to prepare for delays or take alternate routes. This, of course, reduces costs and increases efficiencies.”
Such insight, he continues, helps service technicians become more proactive, rather than simply reacting to situations. With the ability to securely monitor customer equipment and environments in real time via IoT sensors, field service technicians will, in the future, be able to take action before problems arise.
According to Craig Nel, Cloud platform leader for mobile, bots and AI at Oracle Middle East, Africa and Turkey, many companies take monitoring as the starting point for their IoT projects. It is about knowing where assets are (location-based services) and what they are doing (performance-based services). IoT supports these functions seamlessly and has the ability to report remotely report, either when requested to do so or completely autonomously.
“Predictive and preventative maintenance are the next logical steps in realising added value from IoT deployments,” explains Nel. “In many instances, this becomes a phased implementation that starts with an analysis of the performance services, namely looking at parameters such as mileage, consumption of fuel, oils and lubricants, maintenance and service intervals, and so on. Only once a reasonable dataset is gathered can analysis and AI be applied to increase the intelligence of the overall system. This is usually followed by predictive and, ultimately, preventative maintenance.”
Don’t criticise; analyse
Nel believes what we are now seeing in the market is a tendency for manufacturers to push more intelligence down into the IoT devices themselves. This means the devices can start to compare, for example, temperature data with defined parameters. If this falls outside of safe operating parameters, it can trigger a complete shutdown of the asset, or simply reduce the performance parameters.
“All of this can happen within the device, without any external analysis or interaction,” he elaborates. “Clearly this is aimed at processing and reacting to data that requires immediate action. At the same time though, this data, together with a host of other sensor data, will still be reported for additional analysis.
“It is easy to see the kind of cost savings that could be obtained if an asset reports an imminent failure and the intelligent system can predict time to complete breakdown, preventative measures, the closest technical repair station, the most likely procedure required to repair and even availability and location of spares.”
Gouveia adds that many logistics businesses use the capacities of their trucks insufficiently, which has a negative impact on their efficiency. With the help of 3D cameras on the loading docks and suitable analytics software, companies can collect and analyse a variety of data about the loading process. This provides them with important information on metrics such as loading density and speed, fill rate and employees’ loading techniques.
“Furthermore, when the system detects mistakes or inefficiencies in the loading process, it sends a notification to the dock manager, who supervises the process with a tablet or from his desktop,” he says. “Based on these insights, he can intervene to take steps to improve loading quality.”
Streamlining the maintenance process
The majority of field-service operations have recently undergone – or will soon embark on – a re-engineering of their systems to move away from traditional laptop and desktop computers, suggests Gouveia, to the increased use of mobile devices. Mobile solutions include handheld computers, smartphones, tablets and other devices that perform specific tasks such as mobile point-of sale, RFID scanning and signature capture.
“Real-time location systems (RTLS) are key to providing effective tracking data with higher accuracy to perform advanced or predictive analytics,” says Gouveia. “RTLS allow supply chains to collect critical data about assets, including location, stage and condition. In fact, according to Zebra’s recent Manufacturing Vision Study, manufacturers are recognising the value of real-time location tracking technologies and will expand their level of usage from 38% to 61% by 2022.”
Oracle believes that the key to streamlining the maintenance process lies in the increasing intelligence that is being pushed down to IoT devices. Capabilities to run more complex diagnostics, and even trigger preventative actions, are now commonly part of the device, Nel indicates. “Parts can also be ordered ahead of time and delivered to where they are needed, instead of to a central distribution location. Technicians, as well as the required parts, can be dispatched ahead of time to the exact location to meet the asset and perform routine maintenance with minimal disruption to the flow of business.”
The cost savings can be significant. Simply knowing where the asset has broken down (or is about to), knowing which technician is required to perform the repair, knowing what spares are required, where to get them and when they will arrive can produce a massively streamlined workflow that will likely account for significant return on investment.
Adjusting to the changes
In many instances, suppliers are reluctant to maintain high stock levels of parts, says Nel. There are, of course, a number of factors at play here, including the cost of the part, the frequency of orders, the size of orders and so on. And of course, he adds, fluctuations in foreign currency exchange rates. The biggest issue for companies is therefore predicting when a part would be needed and what the lead time would be for it.
“This is where comprehensive analyses of IoT data and the application of AI algorithms come to the fore,” explains Nel. “The ability to predict which part will be required, when it will be required and the supplier where the part can be sourced in order to meet the required deadline for delivery all becomes possible. Systems can even be configured to interrogate a supplier’s system in order to determine stock levels, the likelihood of a stock shortage or delay in delivery, and automatically adjust the order date accordingly.”
The future will be even more innovative
Gouveia believes that automation has many clear benefits for transport and logistics. In the warehouse, automation driven by mobile computers and scanners can ensure that the most up-to-date stock inventory is available for staff. This is important as consumers are now demanding within-the-hour delivery.
“The next stage after smooth warehouse operations is delivery logistics,” says Gouveia. “Here, automation has the ability to help carriers of freight and parcels across ground and air to build a smarter, more connected distribution network, resulting in real-time informed decision-making that improves loading operations.
“Future-oriented decision-makers have revealed that next-generation supply chains will reflect connected business intelligence and automated solutions that will add newfound speed, precision and cost effectiveness to transportation and labour. In fact, surveyed executives expect the most disruptive technologies to be drones (39%), driverless/autonomous vehicles (38%), wearable and mobile technology (37%) and robotics (37%).”
Nel feels that the near future may see opportunities like freight brokerage arising. This, he says, is an interesting concept in the logistics world and may soon see the impact of technology innovation. “The most interesting development here is an Uber-like system in which a mobile app could assist in matching shippers with drivers. The same business model of cutting out the middleman applies, which ultimately could result in savings on shipping.
“Looking further ahead, this could extend to the autonomous-vehicle trend, resulting in even cheaper, safer and more efficient shipping of items across the country. Clearly we still have some way to go before autonomous vehicles take over the mainstream, but it seems both inevitable and not too far off. Most notably, as technology continues to develop, there will only be one outcome: it will make logistics faster, more efficient and, most importantly, more profitable,” he concludes.
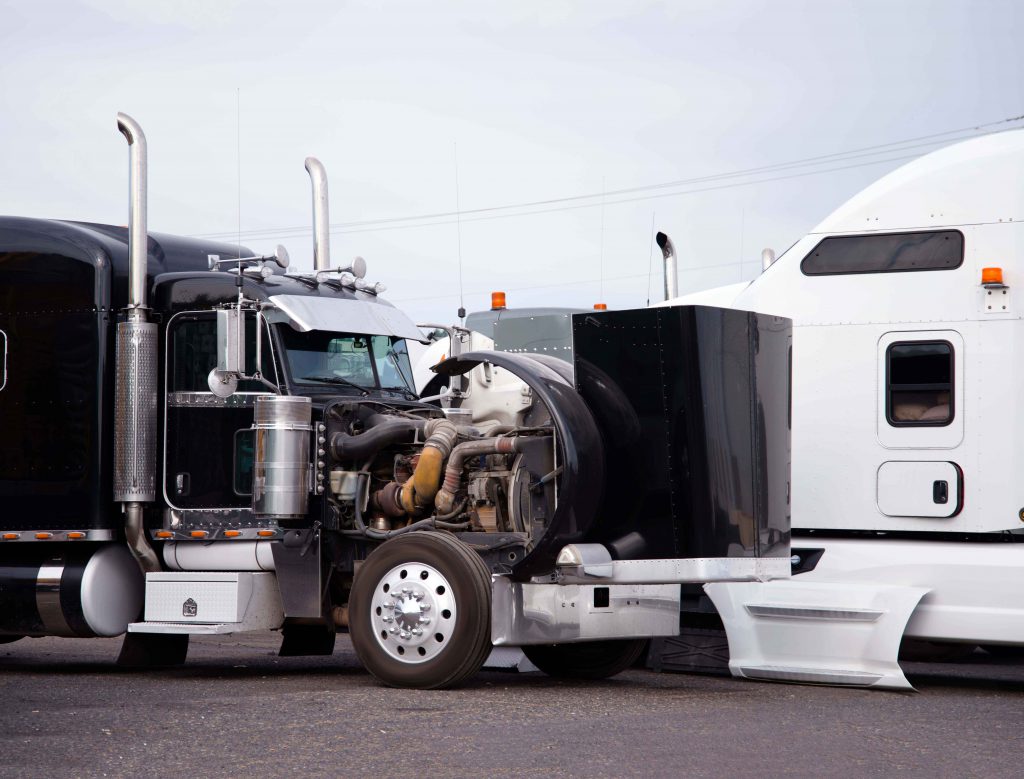